anaflux (attached growth in fluidized beds)
Reading time:In this reactor (figure 3), bacteria are attached to a fine granular material which is fluidised by the upflow of the liquid to be treated, to ensure:
- a maximum biofilm surface area per unit of volume;
- an optimum substrate/biofilm contact.

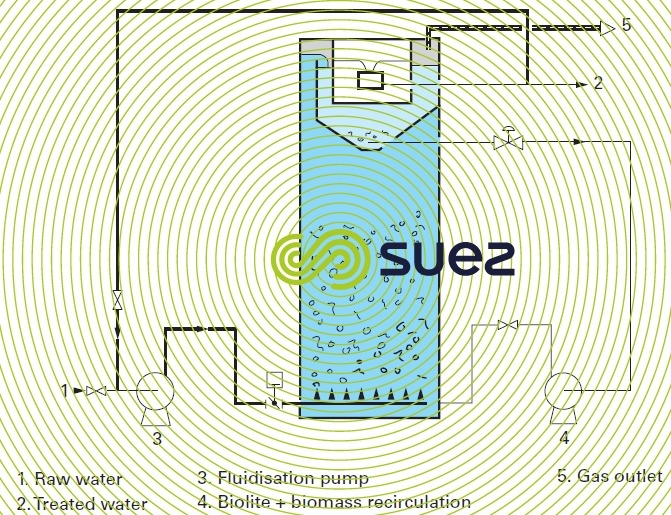

This type of reactor allows the most concentrated growth of active bacterial colonies and can therefore accommodate the highest loading.
A special biolite medium with a NES of less than 0.5 mm was selected, based on the strength of the following properties:
- porous structure (for good biofilm bonding) with high specific surface area;
- low density (reasonable fluidisation velocity ~ 7 m · h–1);
- resistant to attrition;
- production conditions, strictly controlled
design (figure 3)
The reactor can be made of either steel or plastic. Anti-corrosion protection and thermal insulation are usually required.
In order to ensure a good fluidisation of the medium, a velocity of 5 to 10 m · h–1 must be maintained; the process usually requiring effluent recycling. The mixture is evenly distributed throughout the reactor; a three-phase separator located in the upper section of the reactor is used to release gas and to recover and recycle any entrained biolite (carried by biogas bubbles attached to the film).
Gradual colonisation of the material can induce excessive segregation, with the consequence of carry-over of light material out of the fluid bed layer. Excess sludge is detached from part of the medium in a high turbulence chamber, enabling the excess biomass to be removed with the treated water.
applications and performances
The high bed loadings applied to the system (30 to 60 kg of COD per m³ of blanket, subject to a 30% bed expansion) result in relatively short retention times (a few hours), with consequence that preliminary acidification is necessary in most cases.
The main advantages of the process are:
- no risk of clogging of the support material;
- fast start-up;
- compact design;
- accommodation to high flow rate fluctuations.
Depending on the nature of the effluent, water purification efficiency varies from 70 to 85% for COD and from 75 to 90% for BOD5. The Anaflux is suitable for effluents having a COD of 2 g · L–1 or higher i.e. effluents from food industries (breweries, soft drinks, yeast factories, canneries, starch mills, distilleries, dairies,…) or paper industries (paper mills, evaporation condensates,…).

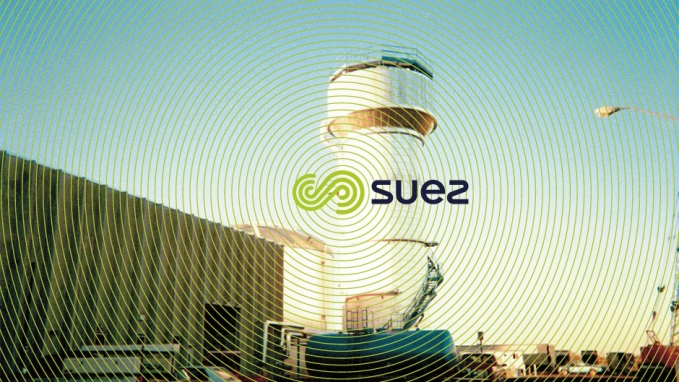

Bookmark tool
Click on the bookmark tool, highlight the last read paragraph to continue your reading later
