analift (mixed digester, settling - thickener tank)
Reading time:This process, also known as anaerobic contact process, comprises a mixed reactor and a separate settling tank, with a sludge recirculation mechanism that can be regulated to keep the sludge concentration in the reactor as high as possible (figure 1).

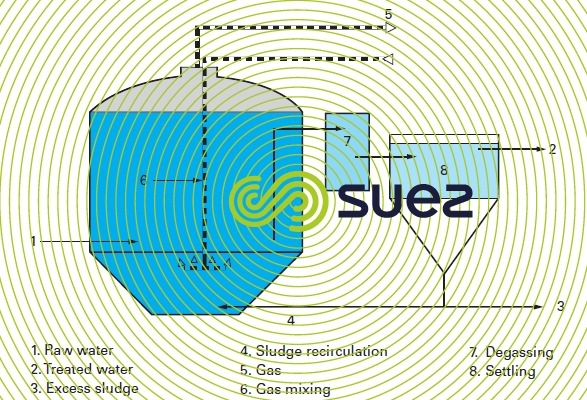

A degasification device is required and installed between the two main pieces of equipment to eliminate the gas trapped in the floc, which hinders its settling.
design
reactor
The purpose of mixing is to keep the reaction medium homogeneous, in order to attenuate the effects of load fluctuations. Mixing is carried out by gas injection through stainless steel pipes (see liquid sludge stabilisation) or by mechanical agitation.
The reactor can be built of concrete, steel or plastic. Internal anti-corrosion protection is often required. Insulation must be applied meticulously to ensure that the requisite temperature is always maintained in the medium. Under particularly favourable climatic conditions, this requirement may be waived.
degasification
The sludge mixture delivered by the reactor travels through a degasification tank, which serves three purposes:
- stilling if required (significant height difference between structures);
- liquor degasifying;
- sludge flocculation as required via slow agitation.
Retention time in this unit must not be less than 20 minutes. Covering requirement and layout of the facility may favour the use of a degasification by partial vacuum.
settling tank
The settling tank is conceived to work as a thickener because the incoming sludge is concentrated. The unit is sized based on its solids mass flow rate, entailing upward velocities of 0.05 to 0.2 m · h–1.
The sludge recirculation rates implemented are typically between 50 and 150%.
applications and performances
When used at low loading rates (2 to 10 kg COD · m–3 · d–1), this process is relatively insensitive to loading fluctuations and, therefore suitable for concentrated effluents (distilleries, canning factories, chemical industries, and paper pulp industries) with, if applicable, high levels of suspended solids and dilute effluent can potentially cause mineral precipitation (sugar beet mills: see washing system lime treatment).
By separating methane fermentation from sedimentation, each unit can be controlled separately for the following purposes:
- transferring sludge from one tank to the other to facilitate maintenance and restart;
- stripping of H2S (a gas produced by sulphate reduction, which can potentially inhibit the methane fermentation process) and gas treatment can be undertaken externally;
- sludge mineral fraction removed after centrifugation (case of sugar mills that apply lime treatment to beet wash systems).
COD removal efficiencies vary from 65% (molasses distillery) to over 90% (sugar beet) and from 80 to 95% for BOD5 removal efficiencies

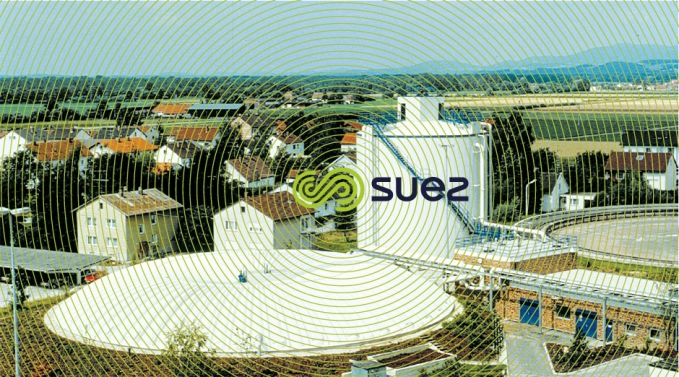


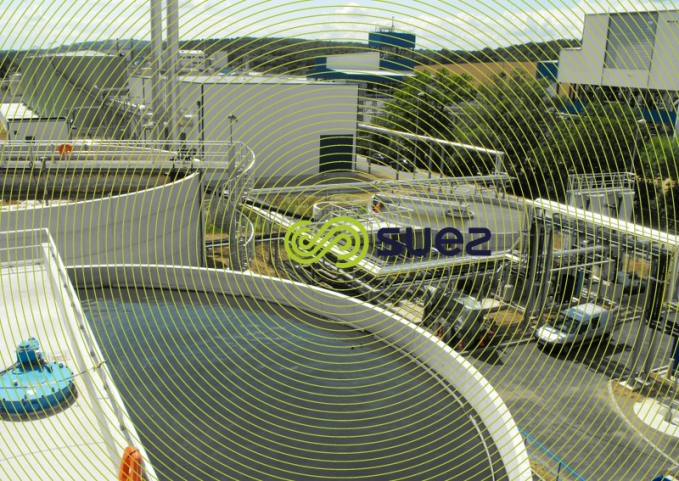


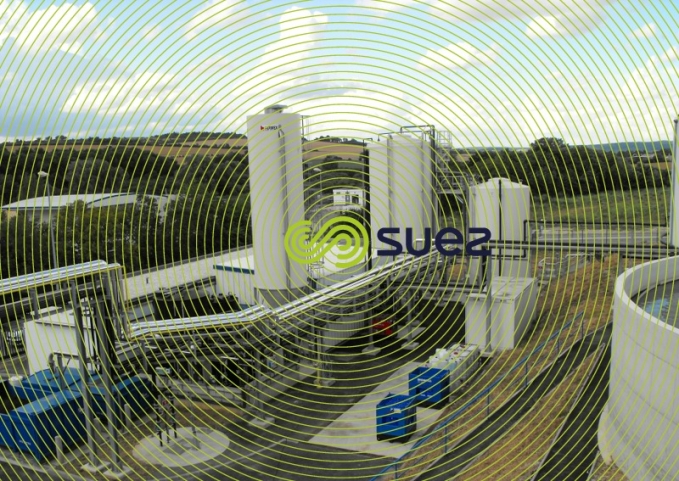

Bookmark tool
Click on the bookmark tool, highlight the last read paragraph to continue your reading later
