oil removers
Reading time:utilisation conditions
Two types of industrial effluent are involved:
- those that are regularly oil-laden (oil production and refining, food oil mills, cold mills, airports);
- effluent that normally has a low oil content but with high accidental peaks (storm water from refineries, heating condensates form storage units, fuel oil powered generating stations, hot rolling mills).
Hydrocarbons will be present in these oils:
- either in the free state;
- or in the state of fine but unstable mechanical emulsions that are more or less absorbed by suspended solids;
- or even, less frequently, in the state of chemical emulsions (e.g. water-based cutting fluids).
Gravity oil removal is only involved in the first two states and depends on:
- the density of the oils which usually varies between 0.7 and 0.95 but that can exceed 1 in the case of some heavy hydrocarbons;
- temperature which, as it rises, will always encourage separation;
- the dynamic viscosity of the oils, that can vary from a few hundredths of Pa·s to over 0.2, a limiting value for some processes.
Oil removal from these different effluents will involve one or two stages:
- preliminary oil removal or removal of floating hydrocarbons; this can be combined with the grit removal stage;
- oil removal which, depending on the target sought, will eliminate dispersed hydrocarbons more or less completely (table 5).

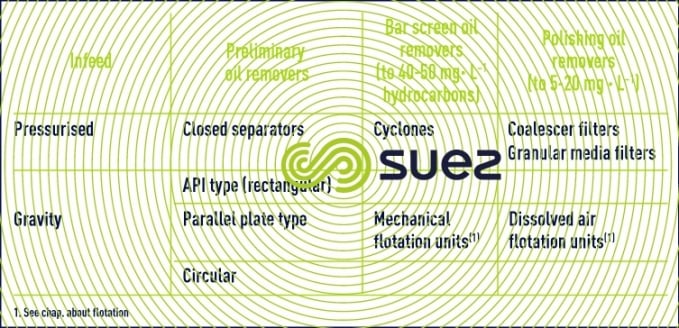

preliminary gravity oil removers
The efficiency of preliminary oil removal units, normally used without any reagents, cannot be quantified:
- hydrocarbon density and the granulometric spread applicable to the droplets and, therefore, the rate of separation with regard to water, is rarely known;
- the nature of the emulsion is poorly defined;
- upstream sampling is virtually impossible.
These units are used to remove huge and irregular inflows of oil and the coarsest of the droplets.
There are three types:
longitudinal separators (API)
Designed according to the 421 standard American Petroleum Institute standard (separation of droplets having a diameter of more than 150 µm), these units are between 1.8 and 6 m wide and have water depths of 0.6 to 2.4 m.
These units are difficult to cover over (necessary to avoid danger of odours emission) and extracting bottom sludge is not a simple matter. SUEZ has improved this product from the Poseidon range to meet the requirements due to the roofing, and sludge extraction. It can build such equipment in its workshops and deliver them fully assembled to the site.

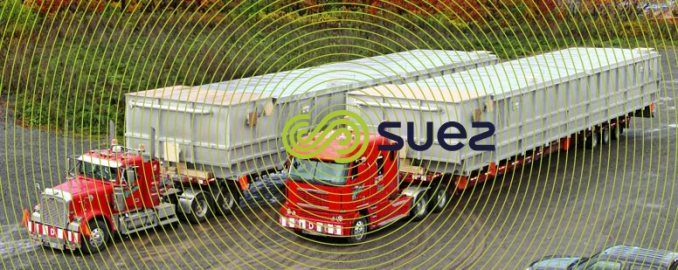

lamellar separators
This is the lamellar settling application with plates made of plastic and that are either flat or corrugated, spaced approximately 4 cm apart and used to reduce contact time from a few hours to 60 or even 30 minutes. These units require more maintenance; they should preferably be used on relatively warm water (avoiding solidification) and low in suspended solids (costly bottom scraping).
As these units are of modular construction, processing high flow rates requires a significant number of modules (each capable of 15 to 30 m3·h–1) with distribution units that are difficult to cover over and skim off.
the degremont® circular interceptor « DCI) »
For specific applications downstream to the oil industry, SUEZ manufactures more compact and easy-to-use equipment thereby avoiding the previous constraints.
- grit is easily removed at a single point
- oil is automatically extracted through a pivoting duct which enables the most liquid of oils to be removed
- it is easy to cover over the unit
- as the equipment makes better use of the height, it is compliant to the API 421’s sizing criteria
This piece of equipment is made out of concrete and steel can be in open format but clients have a tendency to prefer its covered format. Its construction is particularly robust in order to take into account the possible, unpredictable arrival of heavy, sticky substances or significant quantities of oil.

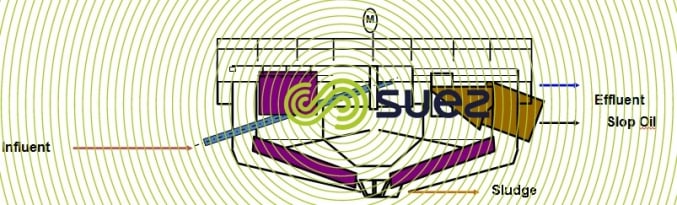


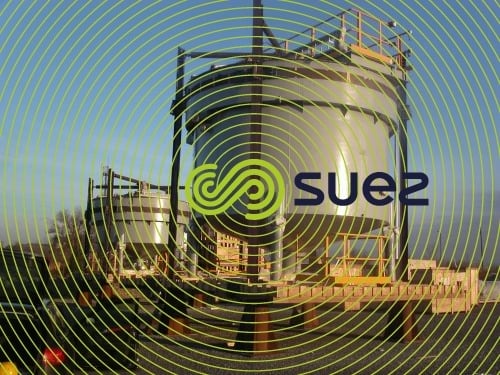




Here, the 3 equipments are covered and blanketed with nitrogen.
Bookmark tool
Click on the bookmark tool, highlight the last read paragraph to continue your reading later
