clarification membrane applications
Reading time:These membranes are gradually replacing conventional clarification systems used to produce drinking water or process water from natural water or recycled water and for pre-treatment in osmosis systems.
drinking water
(see also section membrane processes)
The key of the rapid development of these technologies:
- the use of an absolute barrier which, while the membrane is not breached, produces a water of constant and unrivalled physical and bacteriological properties (protozoa – bacteria and viruses for UF membranes at least).
Therefore, the use of a final remanent disinfectant continues to be recommended: Cℓ2 – Chloramine – CℓO2, for protecting the mains network. However, the demand for chlorine or its by-products remaining minimal at this stage, only very low amounts are required (typically 0.2 – 0.3 ppm Cℓ2). The same applies to the by-products created.
Therefore, we use these membranes:
- as a single treatment stage on water that is lightly laden, particularly with organic matter (TOC < 2 mg · L–1):
- reservoir water (beware of algal bloom) ;
- groundwater affected by the surface (e.g. water from karstic systems …).
- a "combined" treatment stage on low turbidity (< 25 NTU) surface water that is, however, rich in natural organic matter. In this case, submerged membranes combined with coagulation-flocculation and, if necessary, added PAC, can constitute an interesting alternative to conventional direct filtration – ozonation – GAC filter systems;
- as a surface water polishing "tool" after a conventional treatment that includes at least a clarification (sedimentation or flotation) which, properly dimensioned, may not have to be followed by a granular filter, the membrane system taking care of both filtration and disinfection and, if necessary, OM polishing being completed using the extended Cristal process;
- as a means for guaranteeing exceptional quality in terms of bacteriology (especially the elimination of protozoa cysts and viruses in the case of UF membranes) as the final stage in a conventional plant.
desalination and water reuse
Due to the excellent physical quality of their permeate (free of colloids and bacteria), UF systems constitute the choice tool for eliminating particulate fouling upstream from a reverse osmosis plant or from nanofiltration. In every case, the fouling index is reduced between 1 and a maximum of 3 and this applies to any desalination using membranes: seawater, brackish water and especially in re-use treatment lines. However, it should be noted that, typically in seawater treatment, organic matter (macro-molecules) also have to be eliminated and that, in such cases, coagulation-flocculation will still be a necessary pre-treatment phase. The absence of bacterial contamination after an UF membrane will help:
- with controlling "biofouling" but the removal of nutrient substrates and nutrients remains even more critical (see section membrane separation);
- treatment line safety: absolute twin barrier concept in series applications: UF and RO or UF and NF, against all types of pathogens.
In fact, it was in the field of UWW re-use that clarification membranes found their first major wastewater applications, particularly when coupled with low pressure "fouling-resistant" osmosis membranes for, for example, industrial uses (boiler make-up water) or as water re-injected to recharge aquifers, or even to irrigate certain crops, golf courses, parks …
wastewater – MBR ultrafor
Membrane biological reactors ( MBR ) use mineral (internal skin) or submerged organic (external skin) clarification membranes.
The choice between these two membranes must be based on cost (where organic membranes come out on top), operating pressure (where ceramic membranes have an advantage) and above all on the danger of irreversible fouling, or even the destruction of organic membranes by specific compounds contained in the effluent: products that create films, grease that has not emulsified, solvents …
However, these cases are still rare and usually limited to certain IWW. The submerged membrane MBR (Ultrafor) (see section Ultrafor membrane bioreactor) constitutes a good solution for UWW and even for the IWW produced by agri-food industries or by paper mills for instance. They are used :
- to obtain an irreproachable quality making it possible to discharge into fragile environments or even to re-use the water (inclusive of when desalination proves necessary);
- for activated sludge plant refurbishment/extension, especially when available space is tight. In effect, by acting on the mixed liquor concentration during the aeration stage:
- this liquor can either be allowed to nitrify as the plant would only have been processing BOD5. In this case, the Ultrafor would be competing with "combined growths" but with the advantage of being able to adapt to any tank shape;
- or, for an identical F/M ratio, process up to 3 times more throughput by adding (gradually if necessary), modules in a mixed liquor of increasing concentration.
The appeal is that these performances can be achieved with almost no further civil engineering work (clarifiers can even be used for other purposes – upstream or downstream storage) while noticeably improving effluent physical, bacteriological and COD qualities.
The latter effect is illustrated by figure 15 that shows a marked difference in quality, for a typical UWW case, between:

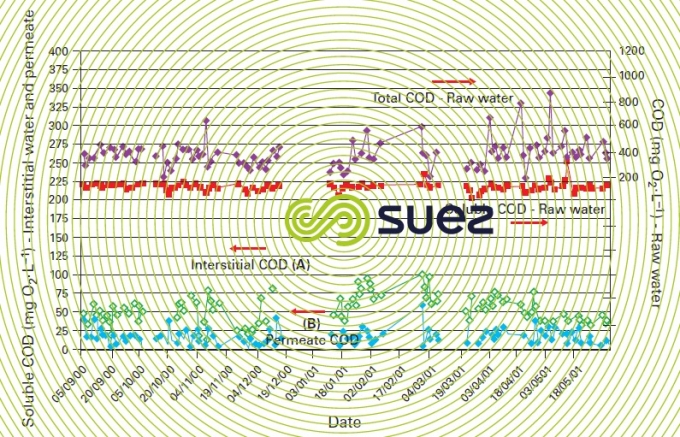

- water obtained from ideal clarification (laboratory conditions) of a biomass in a state of equilibrium in an aerator (see curve A in figure 15): COD of 25 to 100 ppm with an average of 70 (figures typically produced by a conventional clarifier) and
- that obtained from the same biomass filtered through a UF membrane, see curve B, figure 14: a 5 to 50 ppmCOD with an average of 20;
- i.e. a 50 mg · L–1 improvement and lower dispersion; colloids and macromolecules that cannot be settled but that are screened out by UF explain this difference … (these colloids and macromolecules have a very high residence time and are gradually degraded).
It should be noted that, in an existing biological plant where no increase in throughput is required, adding an ultrafiltration stage in "tertiary treatment" will produce a polishing of a quality close to that obtained via an Ultrafor having the same F/M ratio but a slightly higher membrane flow.
Bookmark tool
Click on the bookmark tool, highlight the last read paragraph to continue your reading later
