pyrolysis and thermolysis applied to sludge
Reading time:general comments and definition
The simplified figure 33 can be used to clarify the designations allocated to the various heat processes. Therefore, pyrolysis is the thermal process where the organic matter in sludge is broken down in an environment lacking in air compared to the stoichiometry; thermolysis is the same process when it takes place in the absence of any exogenous oxygen.
This lack of air has the following immediate consequence :
- it dissociates organic matter decomposition from the synthetic gas combustion (forming less NOx);
- it creates less flue gases and removes all or part of the nitrogen ballast from the reducing zones;
- it can adjust the level of temperature at which the organic matter breaks down, independently of the conditions required for satisfactory incineration;
- it creates incomplete combustion (pyrolysis) when this decomposition takes place, thus immobilising certain pollutants in their solid phase and not in their gas phase. When there is no O2 (thermolysis), thermal decomposition processes become intrinsically endothermic. Additional energy will be required by recirculating calories created by downstream energy recycling;
- controls organic matter decomposition and fixed carbon processing in the various zones.

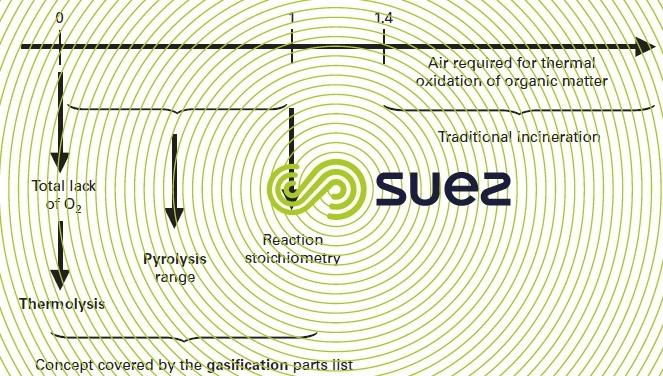

Figure 34 illustrates the origin of fixed carbon. Volatile organic carbon is the fraction of total organic carbon that is determined by the loss by weight at a temperature of 550 °C in a total absence of oxygen. When this breakdown occurs, a substrate remains; this substrate is made up of mineral matter and of a non volatile carbonaceous residue which is treated like mineral carbon.
By order of magnitude, this fixed C represents approximately 15 to 20% of the sludge’s total TOC. During the fluidised bed incineration process (oxidising combustion), this differentiation has no effect. The excess air and transfer coefficients are sufficiently high so that there is no difference between volatile carbon and fixed C combustion within the bed.
The same does not apply to “air-deficient” (pyrolysis-thermolysis) processes where this differentiation is fundamental and can even define the “borderline” between the thermal oxidation processes responsible for destroying fixed carbon on the one hand and thermal reducing process that does not oxidise the fixed carbon on the other.
Another basic difference separates thermolysis from pyrolysis: the type of energy recycling that can be implemented downstream from the thermal process; due to the fact that they take place in the total absence of oxygen, thermolysis processes allow us to use chemical engineering processes to treat the gasproducts created and to produce a synthetic gas or biofuel if the gas is condensed(temperature and decomposition conditions have to be adapted accordingly).
This synthetic gas or biofuel production allows us to postpone its use (appropriate storage facilities). On thermal or technological grounds, thermolysis is only used with sludge that is normally dried to better than 90%.

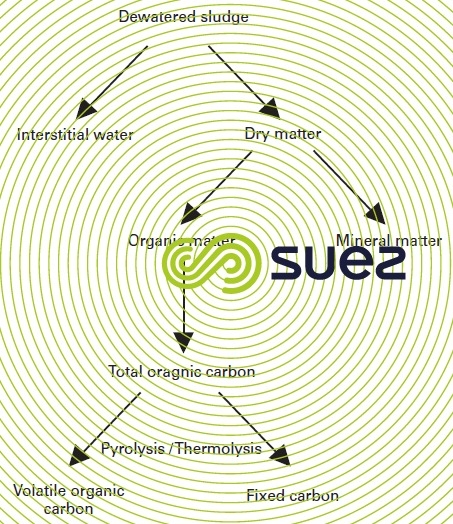

Pyrolysis can be applied to dewatered sludge provided it has virtually reached the self-sufficient heat level defined earlier. Pyrolysis can also be used on dried sludge within the 65 to 90% range. In effect, this is air-deficient controlled combustion that will produce a lean synthetic gas: mixture of raw synthetic gas produced by decomposition and by partial combustion products created by the controlled oxidation of these same products.
This lean synthetic gas is not economically appropriate for any purification whatsoever and its energy must be recycled in-line.
Both processes have similar thermal yields. However, they can be distinguished by the technologies used :
- in most processes, thermolysis involves a twin casing, rotating drum type reactor; the heat is injected exclusively through this twin casing (for information, there are other processes including one developed by Lurgi but that has yet to be applied to dried sludge);
- pyrolysis, as described, usually takes place in vertical, multiple hearth furnaces (superimposed hearths).
Thermolysis and pyrolysis generate a mineral residue made up of mineral ash like that found in dedicated incineration applications, in addition to fixed carbon (overall designated char).
In thermolysis and pyrolysis, char is processed in a separate reactor except when pyrolysis takes place in a multiple hearth furnace within which char processing can also be carried out.
the pyrolysis process in multiple hearth furnaces
Two schemes need to be highlighted :
- case 1 (figure 35) : the reducing decomposition of organic matter and thermal oxidation of fixed C take place in the same furnace. The upper hearths are used for drying if required (should the sludge be wet) and then for pyrolysis; the lower hearths are used to oxidise the fixed C. Both gas flows are extracted separately through the top and bottom of the furnace and mixed in a post-combustion stage where the total combustion of gas residues takes place. Energy recycling takes place dowstream ;

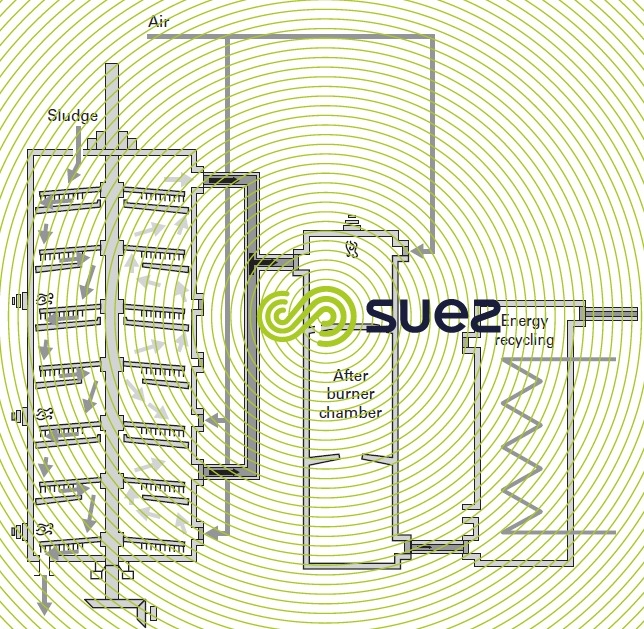

- case 2 (figure 36), used exclusively with dry sludge: the multiple hearth furnace is strictly reserved to the reducing thermal breakdown of organic matter. The “char” is extracted from the furnace and sent to a small classic fluidized bed incinerator where it is incinerated. The mixture formed by the two gas flows is processed in an oxidising post-combustion stage with downstream energy recycling.

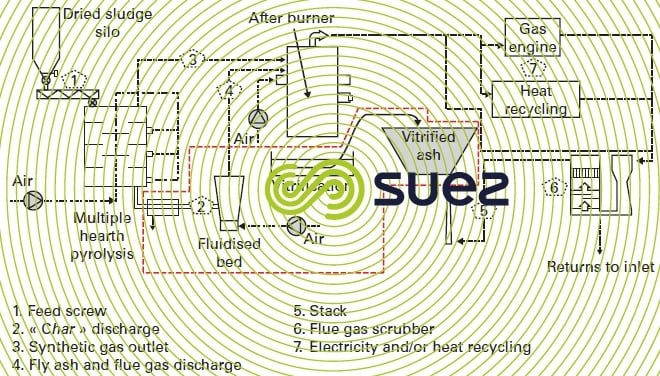

The particular interest of case n° 2 when applied to dried sludge concerns a number of points :
- the size of the multiple hearth furnace is considerably reduced (by a factor of approximately 2). Indeed, the fixed C oxidation kinetics within a multiple hearth furnace are notoriously poor compared to those of a fluidised bed incinerator.
- a more stringent management of the pyrolysis stage where it is easier to hold the temperature to an average level (± 500°C). We can thus better verify the non-formation of dioxins and also the system's reducing conditions (no need for added energy to the upper hearths - no need for drying). We find that the raw synthetic gas delivered by this stage is richer than the previous one and, in the post-combustion stage, enables us to achieve high temperatures:
- the fluidized bed incinerator can be operated in an overflow agglomerant bed system producing a sintered mineral ash that is capable of a high level of stabilisation and, therefore, suitable for final removal comparable to that of clinker delivered by household waste incineration.
- the mixture of the two gas flows (reducing and oxidising) in post-combustion, allows us to achieve very high temperatures (1 200 °C) with almost no dust, which is highly advantageous (no emission of dioxins and/or NOx and no danger of scaling in downstream exchangers and refractories).
The fluidised bed incinerator can be replaced (see red dotted line area in figure 36) by a plasma torch that absolutely guarantees ash vitrification.
The overall energy balance applied to case n° 2 shows the effect of the sludge VM content on energy recycling in the case of co-generation (production of electricity and of residual heat – table 12) and on the recovery boiler (energy transferred to a heat exchange fluid – table 13).

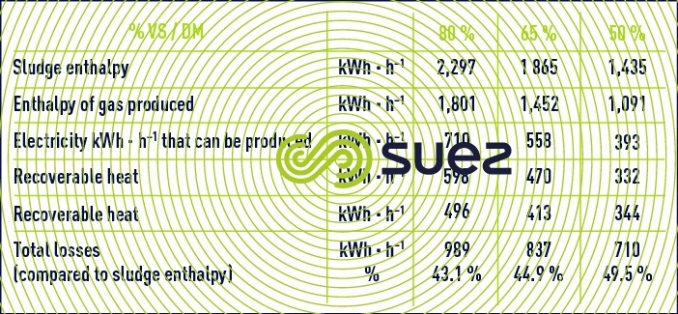


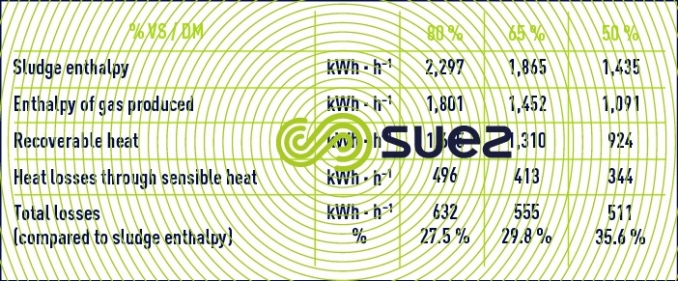

the process involving thermolysis in a rotary furnace with liquefaction
This process applies exclusively to dried sludge and has been developed by the Australian company, ESI. This process tends towards the production of a storable biofuel obtained by condensing the synthetic gas.
The process developed by ESI has the advantage of having had its first industrial application (25 t· d–1 DS) in Australia (Perth), providing accessible feedback.
processes involving thermolysis with the production of syngas
These processes are similar to those described in the previous process. However, higher temperatures are applied in the thermolysis reactor in order to achieve a more advanced "cracking" of organic chains and to produce a syngas that then has to be purified (tars, cyanides…).
This gas purification is a fairly complicated process that has not yet been properly mastered.
Similarly, the original process developed by Lurgi (LR process) is based on a reactor that is self-fluidised by the synthetic gas produced by dried sludge breakdown where the heat input is the sensible heat recovered from mineral ash generated by incinerating a mixture of ash and fixed C. This process comes up against the same problems as synthetic gas production and, as yet, has found no industrial application.
Bookmark tool
Click on the bookmark tool, highlight the last read paragraph to continue your reading later
