using “polyelectrolyte” polymers
Reading time:One must distinguish between:
- polyamine polymers used as coagulants;
- acrylamide copolymer type polymers used as flocculants.
preparing polyamines (organic coagulants)
These are low gramme-molecular weight cationic polymers. They are all sold as slightly viscous to viscous (50 to 10,000 centipoises) solutions. These products can be pumped direct out of a drum or container without any preliminary preparation. This is an undeniable benefit, especially since these products are very stable.
However, good secondary dilution must absolutely be undertaken at the feeding pump delivery point (100 to 200 times dilution in-line) using low salinity clean water (if possible, salinity below 200 mg · L–1).
However, consideration can always be given to preparing these polymers from a stock solution. Nevertheless, in this case, we need to be aware that the product will often be less stable and that this stability will depend on preparation water quality (salinity below 200 mg · L–1 and turbidity below 1 NTU). We recommend using a stock solution that is as highly concentrated as possible (at least 10%). This solution will then remain stable for about 48 hours.
preparing acrylamide copolymers (organic flocculants)
Polyacrylamides are very high gramme-molecular weight polymers used as flocculants. These polymers are mainly available as a powder or an emulsion. They can be anionic or cationic.
Some of these products exist in the form of highly viscous solutions (5,000 to 10,000 centipoises) that can be pumped as supplied with secondary dilution at the feeding pump delivery.
polyacrylamide powders
Certain precautions have to be taken when preparing a solution from powder flocculants:
- solutions, even when diluted, can be extremely viscous;
- if agitated too briskly, flocculants undergo mechanical deterioration;
- flocculants tend to form "lumps" if not properly dispersed under the right conditions.
Preparation concentration : 2 to 5 g · L–1 (depending on product viscosity and pumping limits).
manual preparation
The skid (figure 18) comprises:
- two manual preparation stations; the polymer is dispersed in the first tank and then undergoes maturation in the second, ensuring that the product is properly dissolved:
- an automatic control cabinet;
- a dilution system;
- one or two feeding pumps;
- level gauges.
Preparation time : 30 to 60 minutes, the time taken for the polymer to mature.

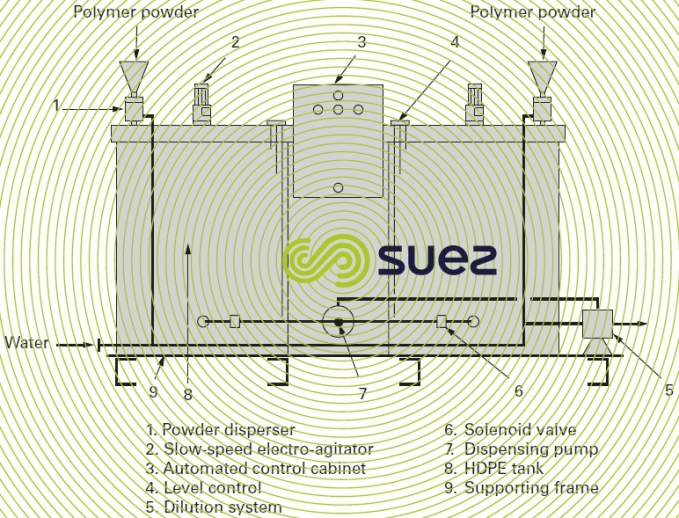

automatic preparation
This type of unit (figure 19) comprises the main tank divided into a series of three tanks with overflow transfer:
- a first tank A, the preparation tank, receives water at a controlled pressure and flow rate, together with the powder measured out by a screw-type feeder, ensuring that the product drops evenly over the disperser; the polymer begins to swell and to dissolve and then flows into the next tank;
- a second tank B, the maturation tank, often equipped with an agitator system; this tank provides the contact time required to allow the flocculant’s molecular chains to "swell" and the product to dissolve;
- a third tank C, the feeder or storage tank, is also fitted with an automatic dispensing control system:
- very high level: alarm (safety);
- high level: timed water switch off + powder switched off;
- low level: timed water entry + powder feed;
- very low level: dispensing pump switched off (safety).

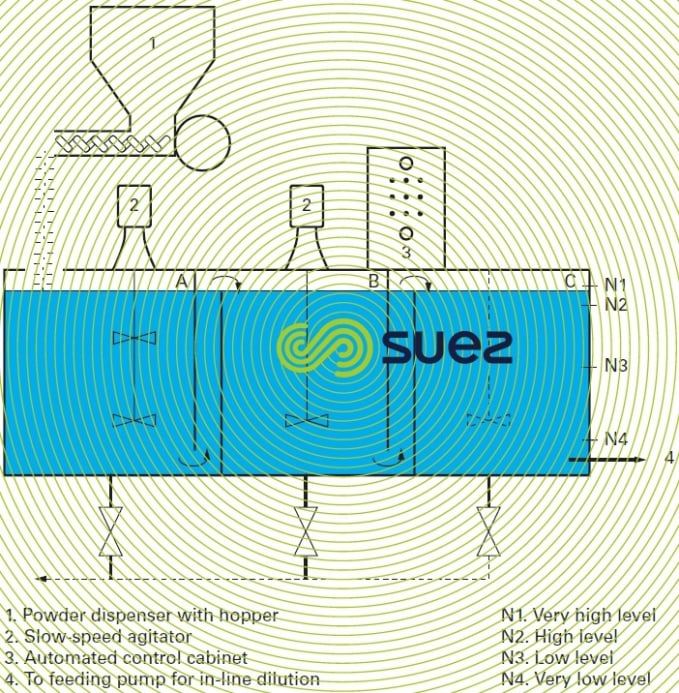

crylamide copolymer emulsion
manual preparation
Manual preparation of emulsions is carried out in the same way as for powder but without a disperser.
The stock solution concentration will be 2.5 to 10 g · L–1 and preparation time is limited to 15 – 20 minutes, so that the emulsion can be inverted before undergoing a second dilution in-line.
automatic preparation
The preparation system (figure 20) comprises:
- a dispensing pump (1) that is used to pump the emulsion out of a drum or a container (2);
- an emulsion inverter or device used to mix the emulsion with a stream of water;
- level control (5-6) in the preparation tank (4) (high level, low level);
- a control cabinet for automated operation.

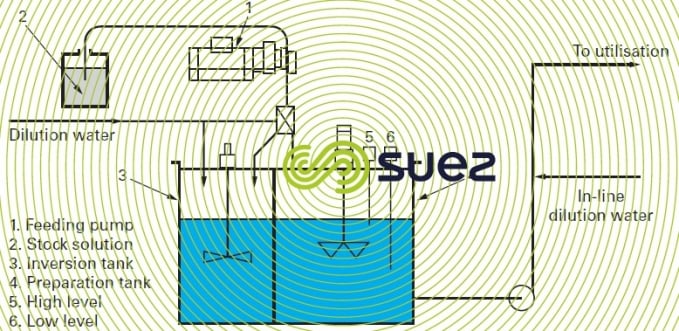

in-line dilution
In order to guarantee polymer effectiveness, it will almost always be necessary to heavily dilute the solution prepared in order to achieve a uniform dispersion of the polymer through the water or previously coagulated sludge; therefore, this dilution will depend on polymer and sludge viscosity and on the mixing energy applied to the system. Consequently, the following target dilution levels will apply:
- 0.5 to 1 g · L–1 in sludge treatment;
- 0.02 to 0.1 g · L–1 in clarification.
This in-line dilution is carried out on the dispensing pump delivery.
Bookmark tool
Click on the bookmark tool, highlight the last read paragraph to continue your reading later
