stainless steel
Reading time:definition and types
By convention, stainless steel is an iron-chromium alloy with a chromium content of more than 10.5%. In effect, beyond this content, under oxidising conditions (oxygen in the air or oxygen dissolved in water will suffice), a thin but stable layer forms and strengthens (see below for increasing Cr, Ni, Mo contents). Depending on its crystalline structure, stainless steel falls into one of five categories: austenitic, ferritic, duplex, martensitic and precipitation hardened.
austenitic steels (table 2)
These steels (the most often used in water treatment applications) contain more than 16% of chromium and 6% of nickel by weight, very often less than 18% of chromium and 8% of nickel. Nickel encourages the formation of an austenite microstructure (crystalline structure, face-centred cubic) that endows it with valuable mechanical properties, high ductility and which make it easy to machine, properties that cannot be found in other stainless steels. Austenitic steels is also the one who, after "duplex" steels, has the best corrosion resistance. When molybdenum is added (up to 6%), this further increases austenitic steel’s corrosion and pitting resistance, especially in a water-based medium that contains chlorine. However, we should note that austenitic steels are sensitive to stress corrosion cracks in the presence of chloride.

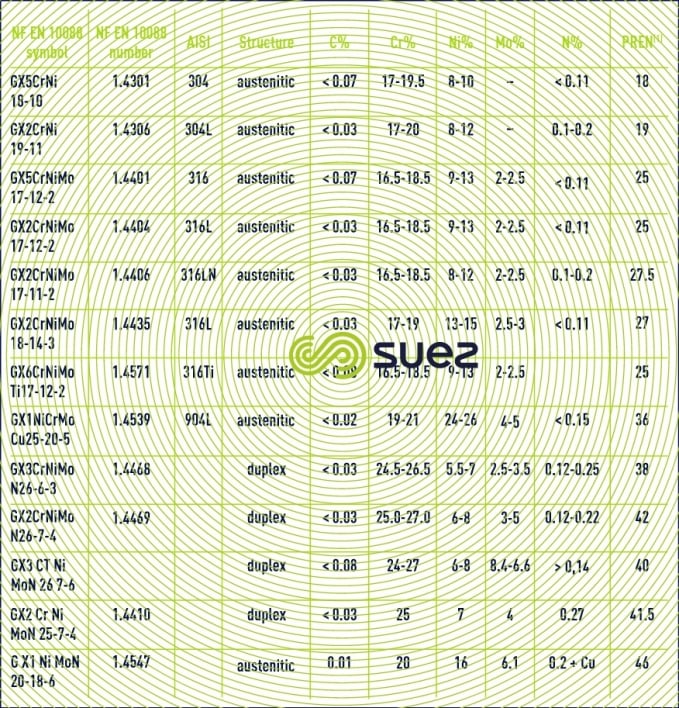

ferritic steels
These steels contain from 10.5 to 27% chromium. Ferritic steels have less valuable mechanical properties, specifically low ductility. Ferritic steels are also less corrosion-resistant than other meterial. On the other hand, ferritic steels are extremely resistant, if not immune, to stress corrosion cracking in the presence of chlorides.
duplex (or austenoferritic) steels (table 2)
These steels contain 18-29% chromium and 1-4% molybdenum together with a regulated concentration of nickel (3.5-7.5%) and/or austenite stabilisers (nitrogen, manganese) that encourage the formation of a balanced ferrite and austenitic structure at ambient temperatures. Each of the alloy’s two phases has interesting properties. The austenite phase produces greater ductility and its mechanical strength is greater than that of each of its phases. High chromium and molybdenum concentrations provide this alloy with excellent corrosion resistance: better than the corrosion resistance of all other types of stainless steel (pitting and stress cracking resistance), which explains the widespread use of these alloys in marine environments: pumps, valves, pressurised pipes, etc …
martensitic steels
These steels normally contain 11.5-14% of chromium together with a higher concentration (0.15%) of carbon than other types of stainless steel. Heat treatment will produce a martensitic microstructure that imparts great hardness and mechanical resistance. Consequently, the alloy can be used in steam turbines, shafts, hard coatings. The low chromium and high carbon contents of these alloys provide them with limited corrosion resistance, the lowest of any stainless steel type. On the other hand, these steels have excellent resistance to stress corrosion cracking caused by chlorides.
precipitation hardened steels
These steels contain from 12.25-18% chromium and 3-8.5% of nickel. These alloys also contain copper (1.25-2.5%) or aluminium (0.9-1.35%) that form intermetallic precipitates after thermal treatment. These precipitates harden the alloy. Most precipitation hardened steels have a duplex structure although some have a martensitic structure. Like martensitic steels, precipitation hardened steels have excellent mechanical resistance and hardness properties. The corrosion resistance of precipitation hardened steel is close to that of austenitic steels but not as good as that of standard duplex steels.
different types of corrosion that affect stainless steels
general corrosion
The entire stainless steel surface can be attacked uniformly when the passive film disappears from the surface without being able to reform. This corrosion occurs when the surface is exposed to reducing mediums.
specific corrosions
Two forms of corrosion (pitting and crevice corrosion) are typical of stainless steels.
pitting corrosion
This corrosion occurs when the passive film is breached or damaged (chemical attack, mechanical damage, presence of microstructure irregularities such as non-metallic inclusions caused by machining). Stainless steel resistance to pitting corrosion will depend on temperature, pH, aggressive anion concentration and on the alloy’s composition and especially its chromium and molybdenum contents. A particular steel’s resistance to corrosion pitting can be evaluated as its chromium equivalent or PREN (pitting resistance equivalent) through the following equation: PREN = % Cr + 3,3 × % Mo + k × % N (table 2 and figure 7) where k = 0 (ferritic), k = 16 (Duplex) or k = 30 (Austenitic).
It is thought that a PREN > 35 is required for pitting resistance in seawater, > 40 in the case of hot and stagnating seawater, > 45 for crevice corrosion resistance.

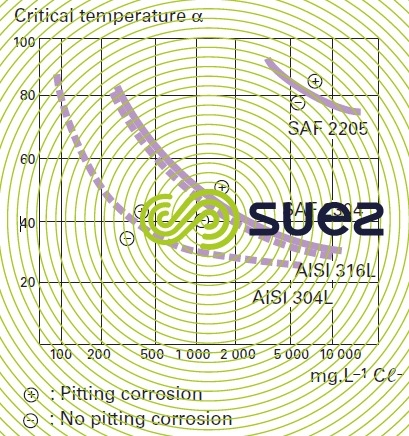

crevice corrosion
This corrosion is a different but serious form of pitting corrosion. A crevice tends to restrict oxygen diffusion over the stainless steel surface, thus preventing surface passivation re-instatement from taking place. Aggressive anions such as chlorides diffuse throughout the crevice corrosion region, creating an environment that has an anion concentration that is markedly higher than in the water mass, capable of significantly lowering pH. Crevice corrosion tends to develop with time depending on anion excess concentration. What is termed the incubation period can occasionally last several months. Once the incubation period is over, corrosion will continue until the crevice becomes blocked up. Layers of deposit will also create conditions similar to those found in mechanical crevices.
There are also other, rarer, forms :
stress corrosion cracking
Austenitic steel is sensitive to this type of corrosion above 60°C in the presence of dissolved oxygen. Residual stress is produced by initial metal forming and welding operations although a good welding procedure will avoid this problem by properly annealing the heated area.
intergranular corrosion in stainless steel
This is primarily caused by chromium carbide forming along grain boundaries, depleting the adjacent metal of chromium, thus rendering it sensitive to corrosion. Sensitisation can be controlled by using low carbon content (< 0.3%) steels or steels that have adequate levels of stabilising elements such as titanium or niobium.
biological corrosion
It can affect steel either by blocking oxygen diffusion or by creating reducing conditions and even sulphur reducing bacteria.
using stainless steels
The main principles to be applied when using stainless steels can be summarised.
when designing equipment
- eliminate dead areas by ensuring that the liquid flows correctly (provisions must be made to blowdown any inevitable dead zones);
- avoid crevices ; if these are inevitable, ensure that they are properly filled in.
When welding stainless steel to carbon steel, the mild steel will dilute the stainless steel at the weld, creating a risk of crevices forming in the weld. In order to avoid this problem, use an appropriate welding rod and suitable welding techniques.
when constructing equipment
- avoid metal-metal contact between stainless steels and carbon steels or low content alloys or other less noble metals in order to prevent galvanic corrosion of the less noble metals;
- use a welding process that will not affect the structure’s corrosion resistance. Select appropriate base metals and welding rods together with a suitable welding technique:
- after forming and before being used, stainless steel components must undergo a mechanical cleaning followed by a chemical cleaning and passivation.
sealing test
Pitting corrosion on stainless steel can occur immediately or in the short term after hydraulic tests when the water used is not of a satisfactory quality.

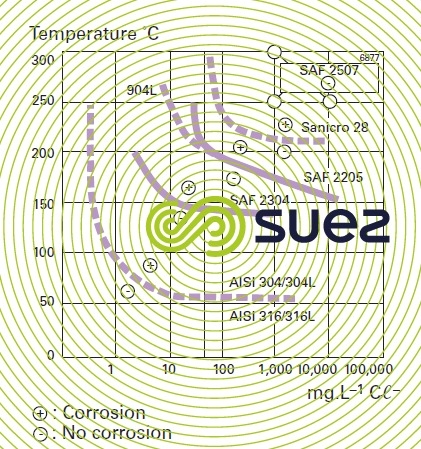

Bookmark tool
Click on the bookmark tool, highlight the last read paragraph to continue your reading later
