membrane plate filter press
Reading time:description-performances
Despite being more expensive, these filters are becoming used more frequently. On the outside, these filter presses look like conventional filters but one of the inner surfaces of each chamber is coated with a polypropylene membrane (case of the integrated membrane plate) or a rubber membrane (attached to the plate and, therefore, interchangeable).The other side of the filter chamber is conventional (see example in figure 45).

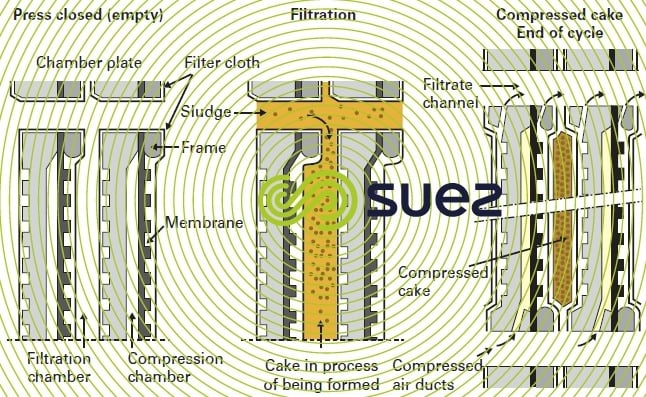

Water or compressed air is used to apply a pressure (15 b) to the membranes.
The following cycle applies:
- filter fed by a pump at a 6-7 bar pressure;
- cake pre-formed under this pressure;
- pump shut down and membranes inflated for 15 to 45 minutes depending on the sludge;
- conventional cake removal.
Unlike the classic filter press, the membrane is able to apply an even pressure over the entire cake surface. Consequently, we obtain better dry solids contents and a much more homogenous cake. These cakes are easier to unload because they contain fewer sticky, wet areas. Therefore, this type of filter makes it easier to adapt to polymer treatment conditions.
Improvements in terms of dry solids contents, compared with the conventional filter, will very much depend on the type of sludge and the type of conditioning involved:
- in the case of mineral conditioning (lime treatment), a 4-5 point improvements in terms of dry solids contents is achievable in many cases;
- in the case of polymer conditioning (therefore, a compressibility coefficient close to 1), the dry solids content improvement is more modest:2 to 3 points as a rule.
Output improvements will also vary:
- on mineral hydrophobic sludge that has excellent filtering properties, a 30-40% output improvement can be achieved compared to the classic filter press;
- on problematic sludge, there is no certainty of improved output capacity (example of organic sludge with polymer).However, the additional unit costs are still justified by the increased ease of cake release.
Membrane filter press systems are more complicated (membrane pressurization fluid is fed separately to each plate) and require more maintenance (membranes replaced at regular intervals).
Cake release must always be supervised (save in a few rare cases of favourable sludge) and, therefore, this filter cannot be designated ‘automatic’.
heated filter press
In this process, heating energy supplements the mechanical dewatering process.
The pressing is carried out in a wholly conventional manner. A heating cycle is initiated as soon as the filtration cycle ends. Calories (water heated to 90°C) are sent to the cake indirectly by the plates themselves; these plates are specially designed with hot water circulation channels that turn them into heating plates.
In order to encourage drying, filtrate circuits operate in a slight vacuum (which assumes total sealing at the joint faces and, therefore, the use of rubber seals on the periphery).
Thorough drying (90% of dry solids contents) is feasible but its not economically sensible (24 hour heating period).
However, partial drying (35 to 45% of dry solids contents) does constitute a possible application (e.g. self-combustion of extended aeration sludge that has undergone polymer conditioning).Heating time will be reduced to a mere 2 to 4 hours. Another advantage is the fact that cake release is improved because the cake easily detaches from the filter cloths.
There are very few such applications at present because the equipment is still expensive and mechanical reliability (sealing) remains a delicate matter.
Bookmark tool
Click on the bookmark tool, highlight the last read paragraph to continue your reading later
