sludge thickening
Reading time:Thickening is the first, and frequently inevitable, step in reducing the volume of sludge extracted from the water line. In fact, it is used to optimise the subsequent conditioning, stabilisation and dewatering stages by reducing structure sizes and operating costs.
Extremely dilute sludge delivered by the water line (usually 99 to 99.8% water)is concentrated to produce sludge containing 90 to 96% water. This sludge is still fluid and, therefore, can be pumped out.
Thickening constitutes an additional investment cost and a source of possible nuisances. However, this is largely offset by savings made on the downstream line:
- reducing the size of anaerobic digesters or of aerobic stabilisation reactors;
- eliminating thickeners downstream from biological stabilisation processes and, consequently reducing the amount of pollution returned to the head of the plant;
- option of extracting dilute sludge from the primary settling tanks, thus preventing fermentation in those structures, generating foaming and bulking (threadlike bacteria) during biological treatment;
- in general, reduced levels of conditioning upstream from dewatering;
- increased output by dewatering units and reduced power consumption;
- very noticeable reduction pumping, transfer pipelines and any intermediate storage tanks (if applicable).
Two processes are used:
- thickening through gravity settling; settling that takes place exclusively by gravity. This technology is usually known as static thickening;
- dynamic thickening: concentration that applies mechanical energy. This is mainly:
- flotation;
- draining/filtration;
- centrifugation.
Depending on the different types of sludge to be thickened, it can happen unknown for these two processes to be combined in the same plant in order to optimise the final mixture’s thickening grade (figure 4). Depending on the limitations set by the downstream system, removing coarse matter, rags, fibres … can often prove very beneficial. It is at this stage in the thickening process that we might find screens, bar screens, press-screens …
A cyclone sometimes has to be used to remove grit from industrial, mineral and sandy sludge: the cyclone will be installed at the inlet to the static thickener, on dilute sludge, in order to achieve the best separation performance.

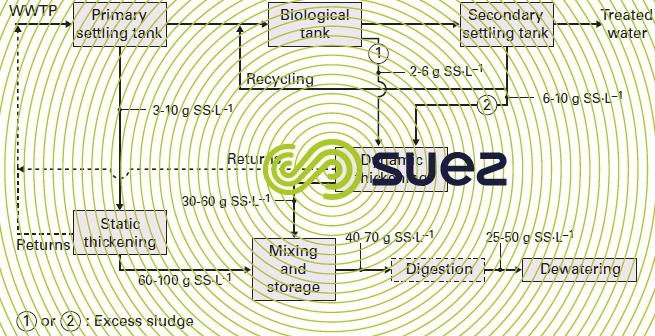

Bookmark tool
Click on the bookmark tool, highlight the last read paragraph to continue your reading later
