sludge recirculation settling tanks
Reading time:In this type of unit, sludge is separated from clarified water in a clarification zone. The sludge is then recycled to a reaction and mixing zone equipped with mechanical (Accelator, Turbocirculator) or hydraulic (Circulator, Thermocirculator) agitators that simultaneously provide energy that is required for both sludge flocculation and recirculation. Raw water to which reagents have been added is injected into the same mixing zone.
These units can be used for clarification only or for precipitating various salts (e.g. CaCO3, CaSO4, CaF2…) or metal salts in the form of hydroxides (Fe(OH)3, Mg(OH)2, Cu(OH)2…).
the Accelator settling tank
The Accelator (figure 16) is the oldest of this type of clarifier; it comprises a central reaction zone (5-6) surrounded by a clarification zone (7). Both zones communicate with each other through the top and through the bottom.
A turbine (4) located in the upper part of the reaction zone, causes the water to circulate towards the settling zone. The sludge deposited in this zone returns to the central zone under the effect of induced circulation (8). The ensuing sludge enrichment produces rapid flocculation.
If necessary, a bottom mixer is used to combine the raw water with the sludge and the reagents. Additionally, this prevents heavy deposits from accumulating and possibly blocking the unit. One or more sludge pits (9) are used to extract the excess sludge in as concentrated a form as possible.
The Accelator IS is a variant comprising a scraper in the bottom section of the clarification zone; this approach is used where carbonate removal is carried out using lime and, in all applications, beyond a certain diameter.

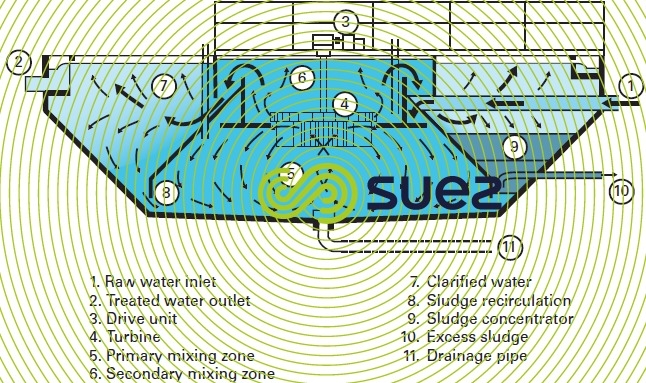

the Circulator settling tank
The Circulator (figure 17) is a very simple appliance that is perfect for use in small to medium sized plants.
This type of settling tank includes a hydro-ejector (3) responsible for recirculating precipitates and/or formed floc before combining the latter with reagents and the water to be treated in the central reaction zone (2). This unit has a conical base to encourage sludge to slide towards the ejector that controls recirculation. Therefore, it does not include any mechanical unit.
Widely found in lime carbonate removal-softening applications, it is also used when pressurised settlement and flocculation is required.
The water’s rising velocity must not exceed 2.5 m · h–1 in clarification mode and 5 to 7 m · h–1 in «pure» softening mode.

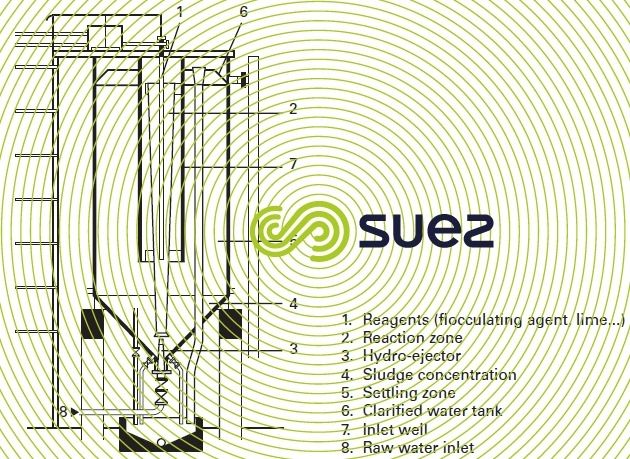

Turbocirculator settling tank
In this unit (figure 18), floc and/or precipitates that have been formed are recirculated by means of an impeller (8) with a specially designed profile. This propeller avoids the deterioration of fragile metal hydroxide precipitates that would not withstand collection via a hydraulic ejector; the propeller enables us to use the same unit for both clarification and softening by tolerating major flow rate fluctuations and maximum velocities comparable to those of the Circulator.
The reaction zone, located in the centre of the unit, provides total control over flocculation and chemical reactions; however, the propeller speed must be adjusted to allow for the more or less fragile nature of the floc formed and, therefore, for the type of treatment applied. A scraper system (5) constantly returns the sludge towards the centre where it is either collected by the recirculation system (2) or routed to the sludge pit from which it is extracted at intermittent intervals (6).

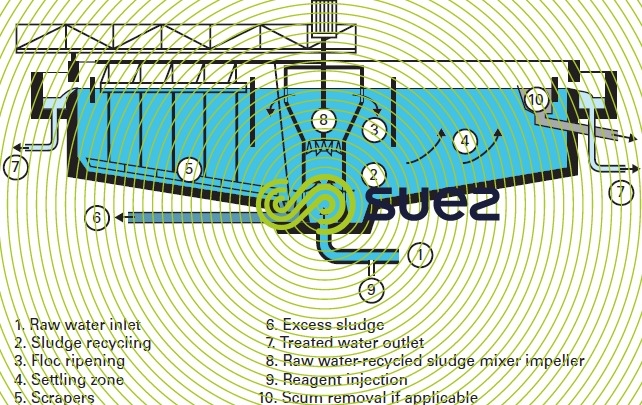


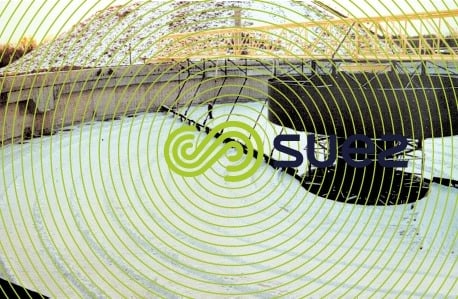

the Thermocirculator settling tank
A variant of the Circulator, this unit (figure 19) is employed when the water to be treated is warm, for instance when using lime to remove carbonate, combined with silicon removal using magnesia, from the feed water of certain medium pressure boilers. It is also used for partial degassing (oxygen).
It should be noted that a variant of the Densadeg is used for high output applications.

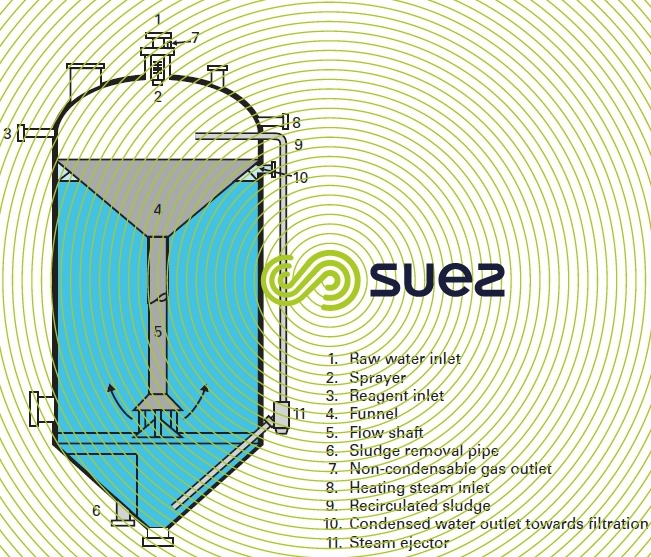

Bookmark tool
Click on the bookmark tool, highlight the last read paragraph to continue your reading later
