static settling tanks
Reading time:By convention, the term «static» is used to designate settling tanks that do not incorporate sludge recirculation or sludge blankets although, in these units, settling takes place on a continuous basis and not in batches.
Depending on the flow rate to be processed, the quantity and type of suspended solids in the raw water, the volume of deposits to be removed and the slope in the base of the structure, the settling tank may or may not be equipped with a sludge scraper arrangement.
In general, static settling is used with:
- river water:
- in very heavily laden water, during the first settling stage (desludging) prior to the main solids contact clarification, preferably after high velocity gradient coagulation using a cationic polymer (when the use of these products is authorised) or an anionic polymer depending on the raw water suspended solids content (see clarification) and by selected scraped type units;
- in small basic water treatment plants in countries that are becoming industrialised, as main clarification after coagulation and flocculation, when the land and civil engineering works are cheap and when the equipment used in other types of settling tanks is too expensive;
- wastewater:
- by far the most widespread application is primary settling irrespective of the flow rate or of the physical-chemical treatment (after coagulation-flocculation) of UWW and of IWW (examples: surface treatment, beet washing water, mining industry, steel mills …) at least for the small flow rates (< 500 m3 · h–1);
- in secondary settling: These units are also known as «clarifiers» (see secondary settling tanks).
The permissible Hazen velocities usually range from 0.5 to 2 m · h–1 in the case of flocculated water; they tend to be higher for granulated matter sedimentation (e.g. scale from rolling mills) or preliminary settling (e.g. desludging).
simple settling tanks without sludge scraping
cylindrical-conical settling tanks
These settling tanks have an almost vertical flow and are used in very low flow rate plants, up to approximately 20 m3 · h–1, especially in the case of IWW purification using physical-chemical methods. Their main application is in the larger plants whenever the volume of precipitates to be sedimented is low but of high density. The slope of the conical section of the unit must be between 45 and 65° depending on the nature of the sludge. This restriction limits their diameter to 6 or 7 m.
horizontal flow, rectangular settling tanks
This type of settling tank is no longer used as a desludger; in this case, the sludge is removed by shutting the unit down, draining it and removing the sludge with a backhoe loader, or, most often using a pressurized water jet. This system needs to be restricted to small plants given the effect of shutdowns and the labour required.
mechanically scraped sludge static settling tanks
A mechanical sludge scraping device is used as soon as the settling surface area exceeds 30 or 40 m². It avoids the need for steeply sloping tank floors required to ensure that the sludge drains out naturally: these slopes can then be reduced (down to 2% in the case of lightweight sludge) and cost-effective construction of extensive but more shallow structures becomes an option.
A scraper system comprises one or more blades that push the sludge along the floor of the tank. These blades are driven by the walkway from which they are suspended (see example in photo 6); this walkway travels either longitudinally by shuttling back and forth (rectangular settling tanks), or by rotating round a central pivot (circular settling tanks); the whole constitutes a scraper bridge.
The scraper system is used to push the sludge into one or more pits from which it is then extracted; scraping the sludge also encourages it to thicken and this feature can even be improved in some cases, by including concentration pits. This sludge is removed more or less rapidly by an automatic extraction system, governed by an acceptable storage time (having taken the dangers of solidification or anaerobic fermentation into consideration).

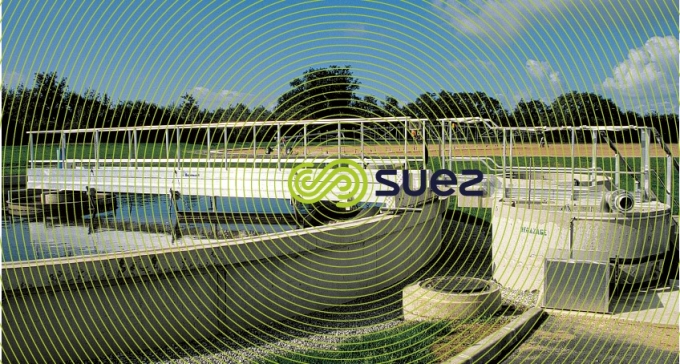

(see secondary settling tanks)
circular settling tanks
Depending on the mass of sludge to be removed, there are several scraped circular settling tanks based on the design of the bottom scraper system (single continuous blade or multiple blades in a «slatted» arrangement) and of the bridge (radial, with or without overhang, or diametral). Additionally, the latter system may have a peripheral or central drive system (photos 7 and 8).
These systems are the most commonly used in UWWprimary settling systems where the degremont® range has two types depending on plant size: the FA settling tank (5 to 24 m diameter) and the P2R settling tank (26 to 40 m diameter). These are peripherally driven units: a reduction gear unit drives rubber-tyred wheels that travel along the settling tank’s peripheral wall (photo 9). The recommended sedimentation rates range from 1.5 to 2 m · h–1 at medium speed and 4 m · h–1 at peak speed. In effect, there is no need to attempt to seek a maximum removal of particulate BOD which is often essential to nitrification-denitrification. The bridge travels at 4 cm/sec. If required, these settling tanks can be equipped with an infrared lamp for de-icing the treadway.

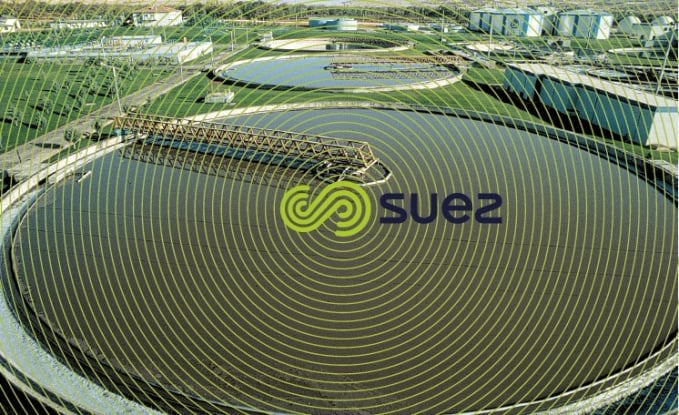


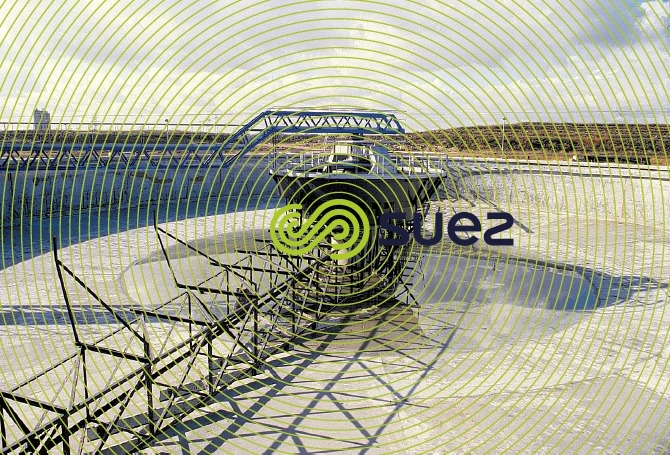


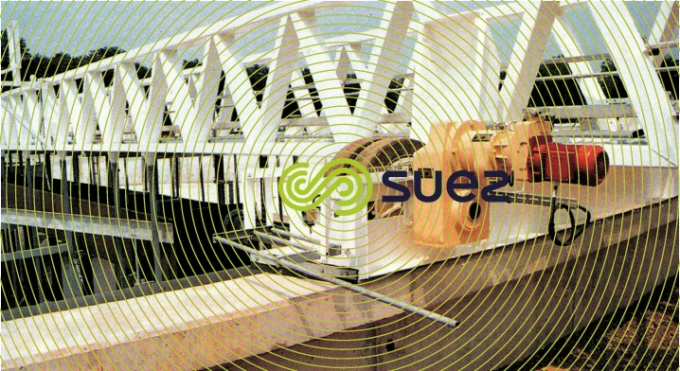

When used to treat natural water, peripheral drive, scraped circular settling tanks may include a central flocculation area (that can also be scraped when treating very heavily laden water) equipped with vertical barriers (figure 7). This type of integral flocculator unit is of interest because of its hydraulics and compactness; it is sometimes known as a clariflocculator.
In the case of large settling tanks (diameter greater than 40 m) or when treating very heavily laden water (e.g. Desludging), the use of central drive systems is also an option. In this case, the reduction gear unit (drive head) Centrideg, photo 10) is mounted in the tank’s axis

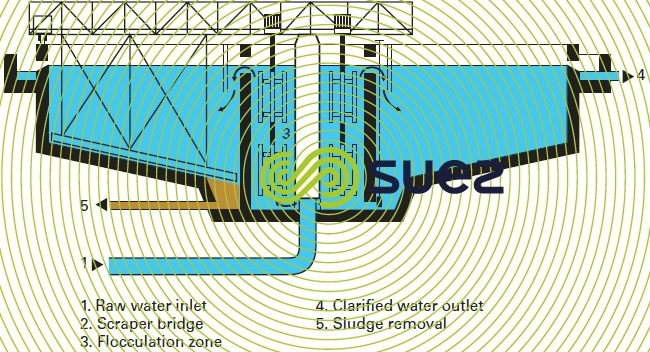


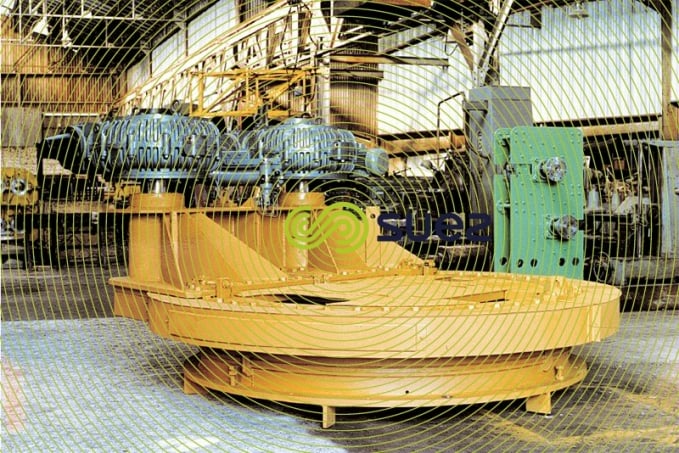

longitudinal settling tanks
Rectangular settling tanks are less widespread. In effect, when several of these tanks are required, they take up less space compared with circular units but are often less cost-effective.
The rectangular settling tank (figure 8) is a horizontal flow tank equipped with a scraper bridge designed to draw the sludge into the sludge pit(s) at the tank inlet. In these cases, the tank floor slope can be reduced to 1%.

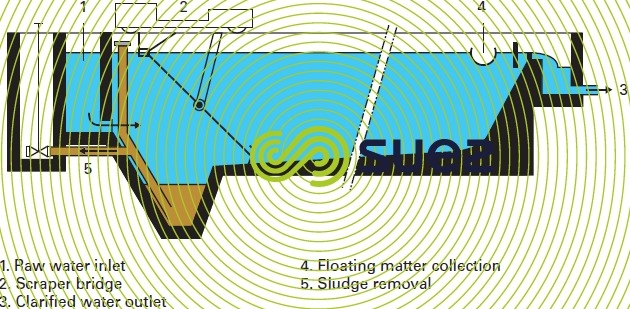

It is important that the water to be treated is evenly distributed across the entire width of the tank inlet using a distribution channel that has weirs or, even better, submerged openings (the distribution must remain satisfactory over a wide flow rate range). Water flows downstream as the settleable matter falls to the tank floor. At the downstream end of the settling tank, water is collected by allowing it to overflow into one or more channels.
The scraper bridge shuttles back and forth, travelling on the settling tank walls. Surface skimming coupled with bottom scraping can either draw scum to the upstream end of the structure or push it downstream as the bridge travels back. There is a maximum permissible interval between two scraper passes past the same point in order to avoid fermentation and the accumulation of heaps of sludge. During the scraping period, velocity will be approximately 2 to 3 cm · s–1. Therefore, lengths must be restricted to between 60 and 80 metres per scraper mechanism.
The shape that produces the best hydraulics has a length/width ratio below 6. In most cases, tank depth will range from 2.5 to 4 m.
The rectangular tank has two drawbacks:
- even when we pay particular attention to inlet distribution, the permissible velocity remains lower than that applicable with the same type of water in a circular settling tank;
- the construction of sludge collection mechanisms is more complicated and their maintenance is more onerous.
Bookmark tool
Click on the bookmark tool, highlight the last read paragraph to continue your reading later
