neutralisation and/or remineralisation
Reading time:neutralising carbonic attack
physical removal of CO2
Potential treatments include:
- cascade: ΔH = 1 to 2 m; residual = 10-15 mg CO2·L–1;
- sprayed: ΔH = 2 to 5 m; residual = 5-10 mg CO2·L–1;
- aeration through diffusion, «medium-size» bubbles: G/L (air flow rate/water flow rate) = 1 to 2; residual = 10-15 mg CO2·L–1;
- forced ventilation in a packing column (see eliminating CO2 in chapter 16): G/L = 10 to 100; residual < 5 mg CO2·L–1;
- fine layer stripping: G/L = 500 to 1 000; residual < 2 mg CO2·L–1;
the target residual content is the content that will achieve an equilibrium between the M-alk. and CaH in the water.
neutralisation using the chemical method
In most cases this is carried out as an injection of lime, sodium hydroxide or sodium carbonate; please refer to the section neutralisation – remineralisation for details of the reactions involved. Complex systems may require several injections at various stages of the treatment. In plants that have total clarification, with settling tanks (or flotation units) and filters, lime is mainly used and injected at a minimum of two points :
- for flocculation pH adjustment (NB in this case, due to the Ca2+ ions, flocculation will be better than when NaOH or Na2CO3 are used); at this stage, lime slurry may be suitable;
- for final pH adjustment to the pHs value; one then needs to use a saturator that delivers clear lime water while screening out lime impurities ; sodium hydroxide can be used as an alternative at this point.
Aggressive CO2 can also be neutralised by filtration through a CaCO3 based granular neutralising product, according to the same reaction and implementing the same technology as for remineralisation using this process.
remineralisation
remineralisation using CO2 + lime
The following reaction applies :


Using this equation, one can calculate that, in order to increase mineralisation (M-alk. and CaH) by 1°F, 8.8 mg · L–1 of CO2 and 7.4 mg · L–1 of pure hydrated lime (or 5.6 mg · L–1 of pure quicklime) have to be injected into the water.
CO2
Industrially, CO2 is supplied in cylinders under a very high pressure and more generally in cooled “low pressure” containers.
In some industrial type installations, CO2 can be obtained by burning gas (submerged burners); however, the impurities generated by incomplete combustion and/or the original fuel, means that it cannot be used for drinking water production.
When used in sea water processing, CO2 obtained by distilling sea water can be recycled and used to remineralise water intended for human consumption (e.g. Alba/Barhein, 43,000 m3·d–1, see figure 43).
lime
Depending on its origin, the purity of lime can vary from 80 to 95%; obviously, this factor has to be taken into account when calculating not only the amounts to be used but also the way in which the product is to be used.
As an illustration, with a 90% “pure” product, if one wants to increase water hardness by 8°F, then 59.2 mg · L–1 of pure lime or approximately 65.8 mg · L–1 of commercial lime will have to be added and this will cause the water to be contaminated by 6.6 mg ·L–1 of suspended solids when the latter are not screened out in a saturator (see further on).
utilisation
There are many applicable cases, depending on the quality of the raw water and of the reagents used :
- with distilled water that only requires added salts, CO2 can be injected and the lime water saturated using in-line mixers, by adjusting the pH to the pHs, or even slightly above the latter (see example provided by figure 43) ;

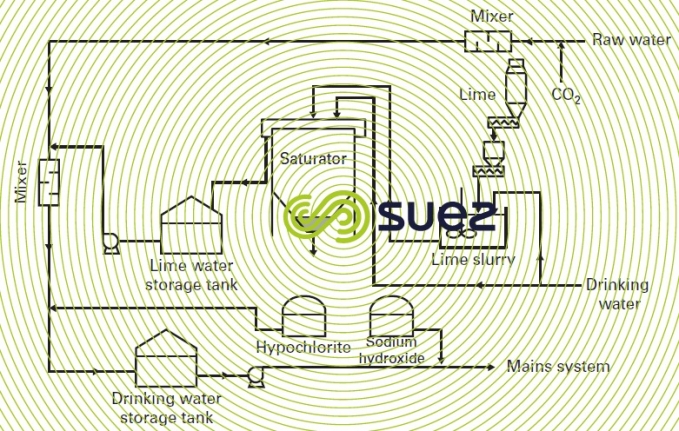

- with a relatively clear reservoir water, after it has been in contact with lime + CO2, all that may be required is simple coagulation through a filter. This filtration stage will be used to eliminate colloid matter and particles suspended in the raw water, as well as limited amounts of organic matter (colour); figure 44 provides an example of this type of system ;

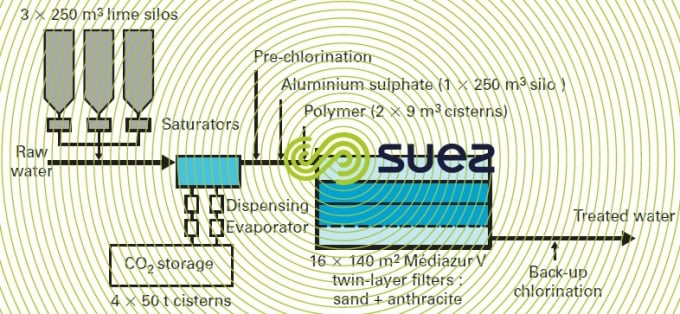

- in water that calls for a complete clarification treatment, the conventional solution was a downstream remineralisation, that is to say following sedimentation and filtration, and lime saturators were used in order to avoid any deterioration to the quality of the treated water (see section lime) ;
- more recently, it has been observed that soft water flocculation posed pH regulation problems. In effect, this water has a low buffering capacity that means that it is rarely possible to maintain pH within the optimum coagulant precipitation zone without having to add a neutralising agent; therefore, the option offered consisted in positioning remineralisation “at the inlet” upstream from coagulation, thereby obtaining the following advantages :
- pH is more stabilised (buffering capacity of the hydrogen carbonates formed);
- when lime is used at the inlet, it can be injected as lime slurry and the impurities contained in the product will then contribute more positively to the ballasting of floc during the clarification stage;
- however, a saturator will still be required for final pH adjustment using lime, but it will be smaller;
- satisfactory coagulation pH control will ensure that organic matter removal is optimised and that the standards applicable to residual dissolved coagulants (especially Aℓ) are more easily met.
On the other hand, a certain number of processes occurring downstream from sedimentation may call for water with a higher pH (precipitation of Mn, biological nitrification of NH4+…). Therefore, one should consider remineralisation positioning: either upstream from the settling tank or between the settling tank and the filters.
A flexible solution consists in anticipating two options by allowing the operator to select optimum conditions depending on raw water properties that will tend to change according to the season.
On this assumption, a minimum amount of CO2 will always be kept at the inlet in order to regulate the pH and a reagent (lime and CO2) and clarified water mixing point will be included upstream from the filters in order to ensure effective pH control and to prevent aluminium from re-dissolving.
contact time
Contact time will vary according to temperature and to the lime slurry or water concentration (usually between 2 and 8 minutes).
process control
The effectiveness of the "lime + CO2" process will be conditional on a very wide range of parameters :
- raw water quality: pH – M-alk. – OM – temperature;
- the quality of the reagents and/or stock solution concentrations;
- reagent flow rate: dispensing pump stability.
Consequently, its use has traditionally been reserved to major surface water processing plants where clarification is compulsory and which, accordingly, have a higher level of instrumentation and inspection personnel.

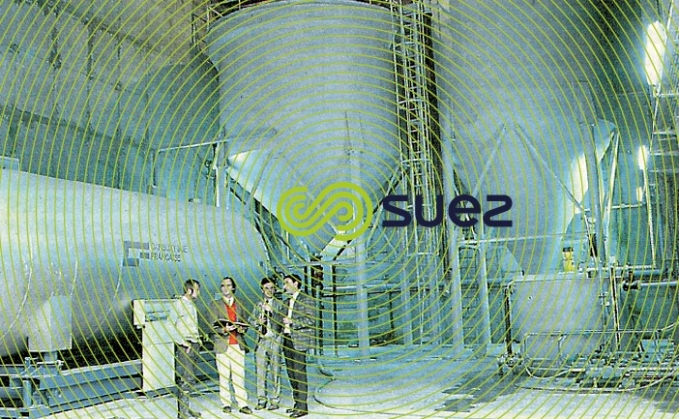

remineralisation using CO2 + limestone
reaction
The following theoretical reaction applies :


In order to increase TAC and TCa by 1°F, theoretically, therefore, one needs to use 4.4 mg · L–1 of CO2 and 10 mg · L–1 of CaCO3.
reagents
The calcium carbonate routinely used in France is a special form with an interesting reactivity associated with its physical state: lithotamine (or maërl) is sold under different brand names including "Neutralite", "Neutralg", "Timalite"… It consists of coral type fossil algae debris (Lithothamniumcalcareum) and major deposits of this material can be found off the Brittany coast.
Other forms of more or less finely crushed limestone can be used. However, the following contact times will need to be adjusted accordingly.
The chemical composition of lithotamine does not vary much: it has a predominating proportion of calcium carbonate, 5% to 10% of magnesium carbonate and a few impurities.
Therefore, the following neutralisation reactions will apply :

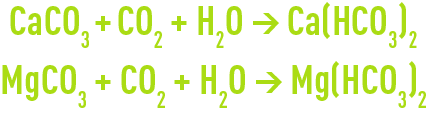
Depending on the CaCO3/MgCO3 ratio and on the % purity of the commercial product, marine limestone consumption can vary from 2.2 to 2.4 kg per kg of CO2 neutralised.
More or less calcinated magnesium oxide based products have occasionally been proposed (CaCO3, CaO, MgO mixture). These products are more reactive and, therefore, require shorter contact times; however, the presence of available bases can lead to a pH > pHs and produce a highly scaling water, especially during prolonged shutdown periods or when the throughput falls below the normal throughput level. In such cases, an accurate check has to be undertaken.
contact
Powdered calcium carbonate can be used by injecting a suspension in water containing CO2 that requires neutralising; however, this method only applies to surface water that requires clarification and the use of a settling tank.
In these cases, a sludge blanket clarifier is particularly appropriate because it concentrates the suspension and allows for more prolonged contact times (30-45 minutes); furthermore, carbonate impurities help to "ballast" the floc, enhancing its settling properties.
More generally, "marine limestone" is supplied in granules that are put in contact in gravity or pressure "reactor-filters" where the water to be treated flows through the filter medium. The efficiency of this type of system depends on :
- the reactivity of the product used (porosity, density);
- particle size;
- temperature;
- the raw water’s initial M-alk.;
- contact time.
Figure 45 illustrates an example of the calculation charts available for dimensioning granulated marine limestone reagents (for a 1 to 2 mm particle size range). The amount of CO2 to be neutralised is established on the basis of raw water quality and target mineralisation and the graph provides the minimum contact time applicable.

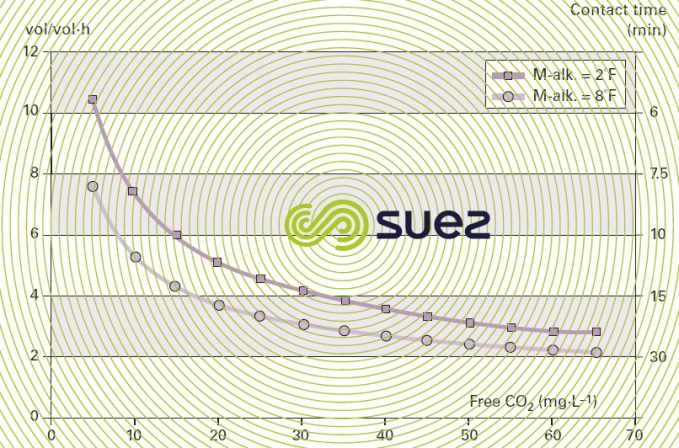

The result is expressed either as contact time (minutes) or as vol · vol–1·h–1. In practice, it is advisable to establish contact times experimentally in each case, given the wide range of parameters that have to be taken into account: temperature, the water’s M-alk., the contact method, the format of the medium (powder, granules etc) and, above all, the permissible CO2 residual value because it is extremely difficult, unless we use an infinite contact time, to obtain zero aggressive CO2 residue.
In practice, knowing that the best that can be achieved is an equilibrium for 0.1 units of pH and whereas most technical specifications demand better than this (pH = pHs + 0.1 to 0.2), the recommended approach is to target a pH that is 0.2 to 0.3 units lower than the pHs at the filter outlet (thus leaving 1 to 2 mg · L–1 of aggressive CO2) and then sodium hydroxide will be used to make the final pH adjustments (final neutralisation).
The changes in the water's M-alk.-pH pair can be monitored using the "Calcograph" chart (please refer to figure 46 for an example).

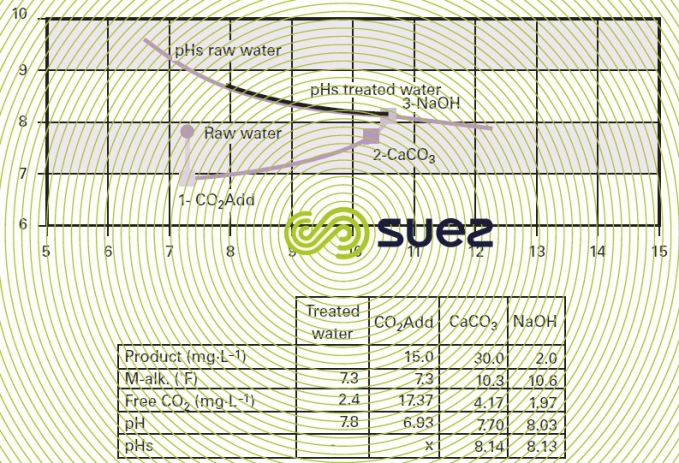

marine limestone consumption: autonomy/backwash
The fact that the product used will dissolve as time passes generates two consequences :
- as the product volume decreases, so does the contact time; therefore, scheduled recharges must be considered and these must be calculated according to the CO2 to be neutralised;
- as the granules gradually dissolve, fines are formed and they tend to clog the material, requiring regular and effective backwashes (air + water washes).
supplementary treatment: disinfection
When limestone neutralisation is used, this can give rise to a deterioration of the bacteriological quality of the water produced (porous materials are easily colonised).
Therefore, one must:
- check the bacteriological quality of the product when delivered after storage;
- at a fixed frequency (at least once a week) carry out an efficient backwash without taking pressure drops into account;
- incorporate a downstream disinfection tank;
- (if necessary) inject chlorine upstream from the reactors or when a backwash is being carried out.
plant inspection
The "CO2–marine limestone" remineralisation system has a major advantage over the "CO2–lime" system: it is only conditional on the amount of CO2 (not always necessary) and there is no danger of any overdosing likely to create heavily scaling water.
Therefore, it is particularly well suited to small units supplied with drilling water where the flow rate will often fluctuate.

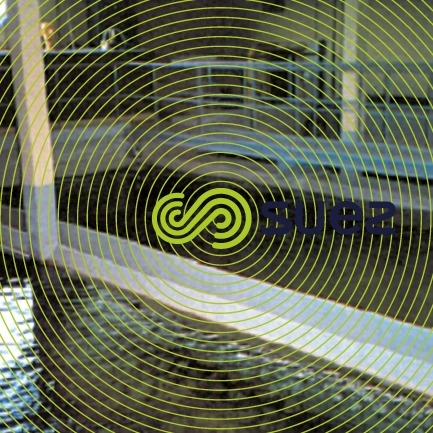

process limitations
Drilling water will often contain dissolved metal ions (Fe2+, Mn2+) that may precipitate when in contact with the atmosphere and when the pH is raised. The hydroxides or oxides that are formed will block the pores of the medium and delay its dissolution.
The same may apply to coloured water that is heavily loaded with humic acids: these may precipitate as metal compounds or as calcium salts that give rise to the same problems.
In such cases, preliminary iron or manganese removal processing using the physical-chemical or biological method (see sections Iron removal and manganese removal), or humic acid coagulation with an iron salt followed by a minimum of sand filtration, will be required before proceeding with remineralisation.
reagent consumption
Table 12 presents the consumption of various reagents deemed pure together with their mineralisation action on water.

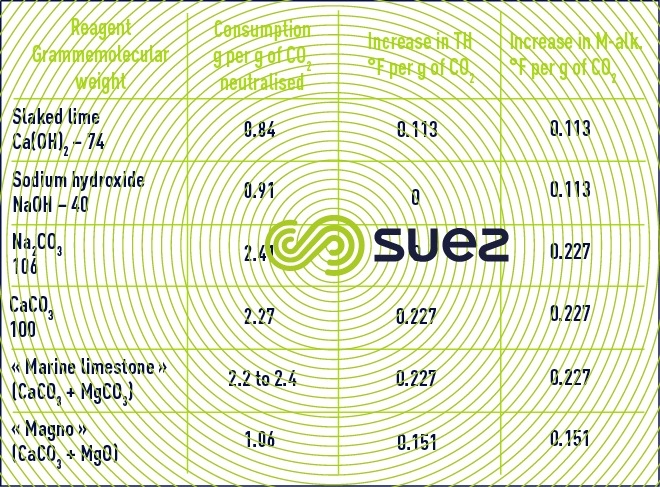

Bookmark tool
Click on the bookmark tool, highlight the last read paragraph to continue your reading later
