effluent generated by ore refining units
Reading time:In this section, we shall focus only on systems located on the site of a mine and where mine drainage water is treated separately.
In this case, we are faced with more complex problems and each case has to be examined individually; in effect, everything depends on the ore being processed and on the more or less advanced refining taking place on the site.
Typically, high levels of acidity and heavy metals will be treated by precipitation and sedimentation, producing a quality treated effluent that can be directly discharged or even recycled to the process. This particularly applies to copper, nickel and uranium mines.
In all cases, it is critical to establish the optimum pH and the precipitation conditions, especially when dealing with specific pollutants (arsenic, antimony, selenium…) or to comply with very stringent standards for metals or radioactive waste. In many cases occurring in the USA, very stringent standards have been satisfied: 1 to 20 mg · L–1 of Cu, Zn, Pb for example (even 1 to 20 ng · L–1 in the case of toxic metals such as Hg or Ag), with a view to discharging the water into rivers or lakes used for leisure activities or which serve as drinking water supplies.
There will occasionally be problems associated with the COD of effluents created by various reagents used in the process and that can inhibit precipitation and/or flocculation.
In many cases, the acid is sulphuric and also requires gypsum to be precipitated.
Massive amounts of lime then become necessary, producing pH levels above 10, enabling heavy metals such as Mn, U and Ra to be removed at the same time.
Among the scenario causing problems, we have the simultaneous presence of major quantities of manganese which, if they are to be properly oxidised (without expensive oxidants) and precipitated, require a high pH; and amphoteric metals such as aluminum which becomes insoluble at neutral pH levels and re-dissolves at the optimum pH for manganese removal. Such a scenario is illustrated by the graph in figure 69 that shows that, even in the presence of iron, manganese requires a pH > 9 for it to be properly removed whereas aluminium will be eliminated at a pH < 7.5. A two-stage clarification system will then become essential such as the one used in the plant constructed at Pinal Creek, Arizona where two Densadeg (one with a 6.5 pH and the other with a 9.2 pH) followed by Greenleaf filters are effectively reducing all metal contaminants – photo 42 (photo ODI).

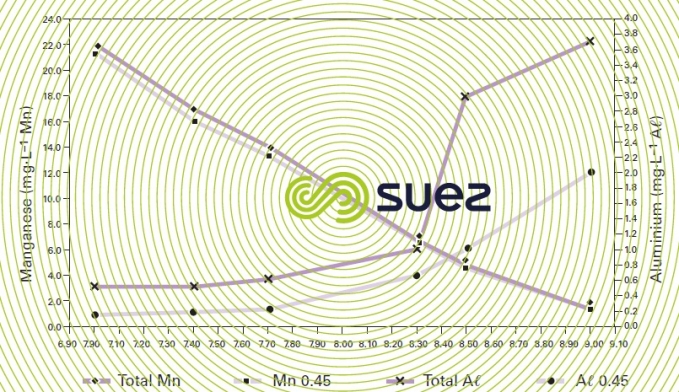


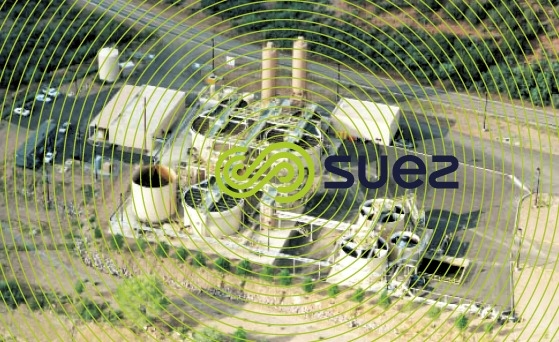

In effect, each mine and each refinery unit are specific cases that have to be diagnosed and designed separately according to the processes and limitations involved.
We give below two examples of effluent recycling at copper refinery plants:
simple recycling
The processing plant comprises a system for neutralising acid effluents with gypsum precipitation and sedimentation. The overflow from this unit undergoes a second neutralisation with the process general wastewater where metals are precipitated and a specific precipitation agent is added before clarification.
The treated effluent is partly recycled to the process.
recycling with a superior water quality
Process effluents are sent to a large capacity storage lagoon with pre-neutralisation using lime at the mine, thus allowing a proportion of the gypsum formed to be settled.
The effluent is sent to the treatment plant where it undergoes neutralisation using lime, completing gypsum and metal precipitation (2-hour contact time) before being clarified; the effluent is filtered through two stages of sand filters before the reverse osmosis unit.
In such cases, pilot trials need to be carried out initially in order to check that the system is operating correctly (in terms of the interference caused by the presence of precipitation inhibitors at the neutralisation stage and of an anti-scaling agents dispensed during the reverse osmosis stage to prevent gypsum precipitating as is concentrates on the membranes).
The quality of the treated water will then be excellent, virtually demineralised. It can be in any of the plant’s process units.
Bookmark tool
Click on the bookmark tool, highlight the last read paragraph to continue your reading later
