specific effluent systems
Reading time:coke plant ammonia liquor
The wastewater treatment most commonly used includes:
- thorough tar removal via sedimentation and filtration, with addition of an organic coagulant;
- steam stripping of volatile ammonia followed by pH adjustment with sodium hydroxide, stripping fixed ammonium (often carried out in two stages in the same column);
- activated sludge biological treatment to remove BOD, phenols and thiocyanides. A nitrification-denitrification treatment is feasible subject to a few precautions that first need to be evaluated by testing (absence of inhibitors);
- tertiary physical-chemical treatment if necessary for residual colloidal COD reduction.
We should also note that stripping can also use free ammonium to blowdown the gas scrubbing water closed system.
Figure 55 shows a typical ammonia liquor wastewater treatment system, including a thorough nitrogen treatment.

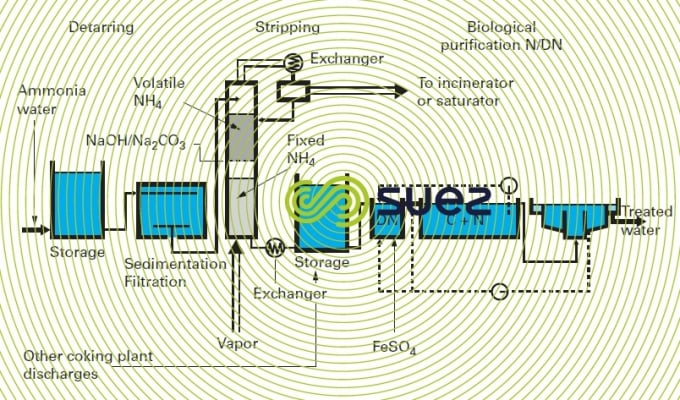

water from an integrated cold rolling unit
This unit processes coils delivered by the hot rolling mill and used to produce metal sheets for the automotive industry, for metalworkers, thin metal sheets for drinks cans and the food canning industry, metal sheet for household appliances, etc., and usually includes:
- pickling that is most frequently carried out with hydrochloric acid;
- cold rolling;
- the various finishing units (galvanising, electro-zinc-plating, tinning, organic linings).
The main pollutants encountered are pickling acids, dissolved metals, lubrication and rolling oils, and highly alkaline specific degreasing baths. This effluent must be segregated at source so that specific pre-treatment can be applied whenever necessary.
Overall treatment of these effluents usually includes:
- recovery of spent hydrochloric acid which is regenerated by screening before being recycled in the process;
- recovery of the cold mill concentrated emulsions that can be processed by evaporation or by chemical breaking (depending on quality) or eliminated via an external system (e.g. cement plant). Evaporation residue can be incinerated and the condensates routed to the alkaline effluent flotation unit in a general process water treatment plant;
- spent degreasing baths are recovered for storage and delivery at low flow rates for dilution in rinsing effluent;
- segregating acid and alkaline systems allows alkaline effluent to be treated by flotation (rinsing and spent baths distributed), the overflow being routed toward the neutralisation system that will utilise the acid effluent (without concentrated baths);
- final sedimentation after flocculation will result in optimum effluent clarification before discharged.
This waste stream can be completely recycled with the addition of:
- an attached growth biological treatment (Biofor type);
- softening (which, most of the time, already forms part of process water treatment); any make-up water will be added at this point;
- filtration to remove suspended solids;
- reverse osmosis to remove most of the salinity and residual COD, allowing the effluent to be recycled through the plant’s ion exchangers or any other clean water application.
Figure 56 illustrates a general wastewater treatment design for a complete cold rolling unit.

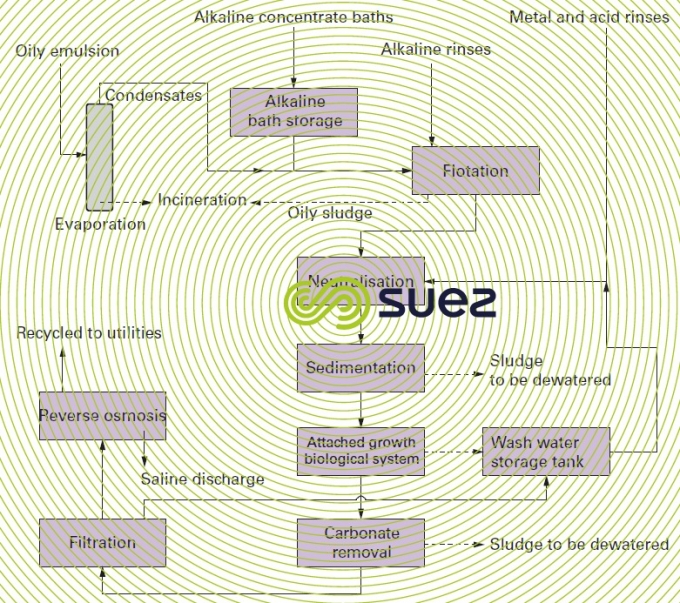

This approach conserves a substantial volume of water, total consumption being reduced to approximately 0.5 m3·t–1 compared to 1.6 m3·t–1 if the neutralisation/sedimentation phase is omitted. This system allows the sole discharge of the brine produced by reverse osmosis (high salinity but relatively little other contamination) and sludge produced during the various treatment stages. Some of this sludge can be incinerated.
Bookmark tool
Click on the bookmark tool, highlight the last read paragraph to continue your reading later
