production
Reading time:Treatment of oilfield water
"Oilfield water" or "produced water" (because the water often rises from the oilfield in the form of an emulsion with the crude oil) is separated in water knockout tanks before preliminary oil removal (hydrocyclone in particular offshore or lamellar separator CPI, Corrugated Plate Interceptor type onshore) and a final polishing treatment that will depend on its end use (figure 24) and on local discharge standards :
- offshore discharge via mechanical flotation ( HC < 40 mg·L–1), dissolved air flotation or coalescence ( HC < 10 mg·L–1); the latter should only be used in cases of very low suspended solids levels (minerals, waxes, solidified heavy hydrocarbons, etc.);
- reuse for re-injection after degasification if necessary and sand filtration.
Reinjection is preferable because it not only avoids any discharge into the sea but avoids the evolution of bacteria, especially sulphur-reducing bacteria, and any chemical incompatibility with reservoir water (often inevitable when injecting seawater). Nor does it usually require water to be de-oxygenated; however, it does require thorough oil removal (1-2 mg · L–1) and filtration.

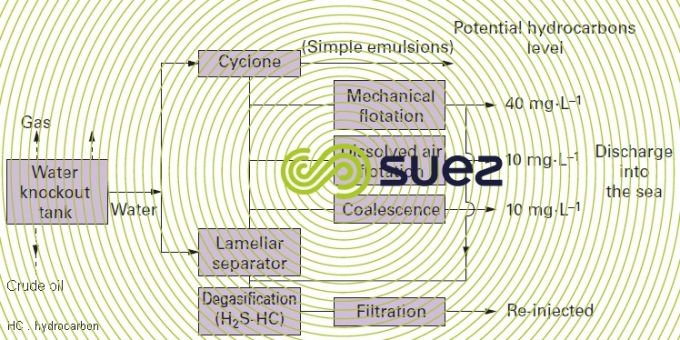


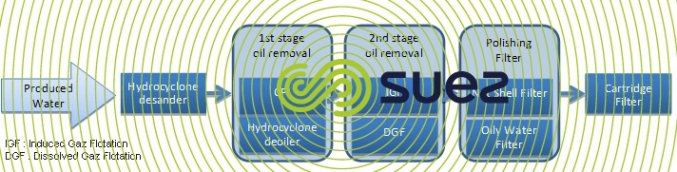


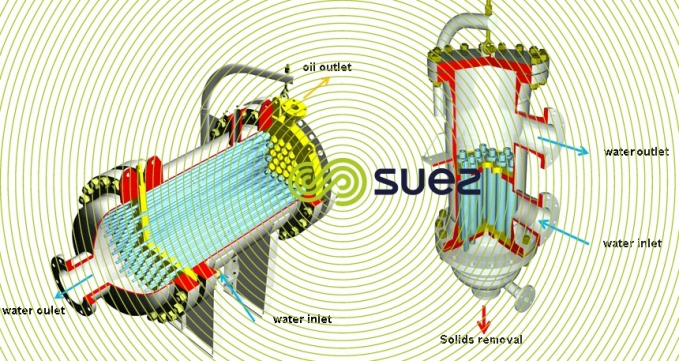


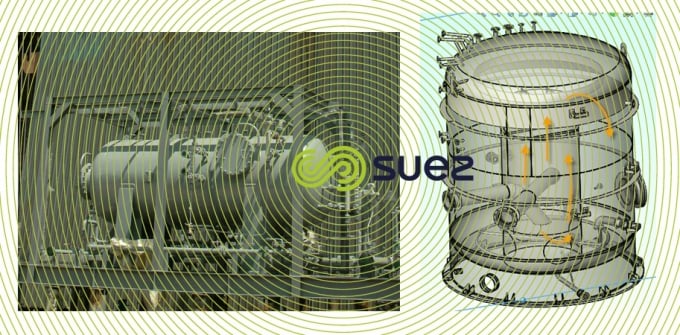

The 3D diagram corresponds to an onshore oil facility in Irak which includes a first oil separation stage using a CPI, a second oil separation stage using mechanical flotation and a polishing stage using a walnut shell media filter. The facility’s flow rate is 530 m3/h and is capable of reducing oil concentration levels from 2000mg/L to 10mg/L by trapping 98% of suspended particles larger than 5µm.

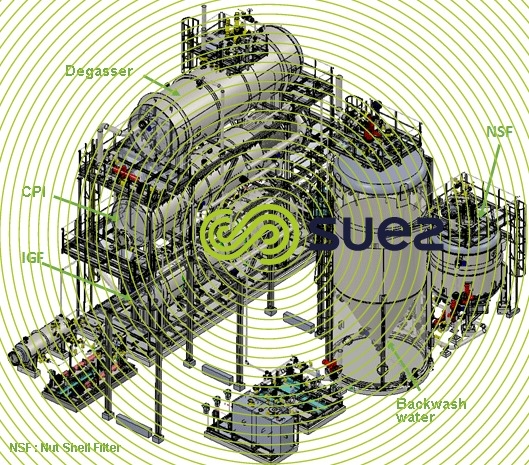

Gas fields also produce water which needs to be treated. This water does not come from gas extraction operations themselves but from the regeneration of MEG or TEG (Mono or Tri Ethylene Glycol) used for dehydrating gas.

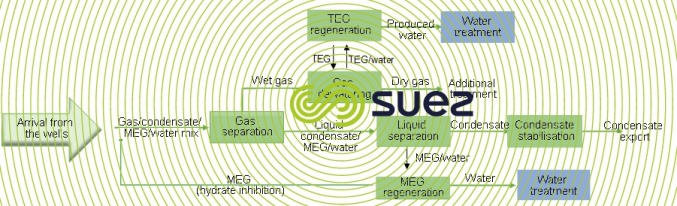

Unlike water produced in the oil fields, water from gas fields does not contain SS or dissolved salts. However the content in oil, BTEX (Benzene, Toluene, Ethylbenzene, Xylene), phenol and more generally organic compounds is significant and requires a treatment level which may be very advanced depending upon the discharge standards required. The treatment stages generally include oil separation, removal of toxic organic compounds, a biological treatment process and a potential polishing process.

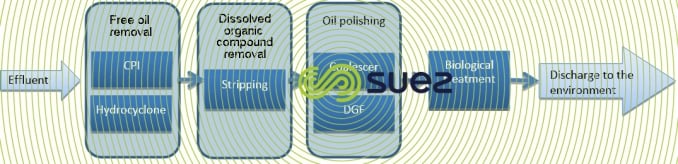


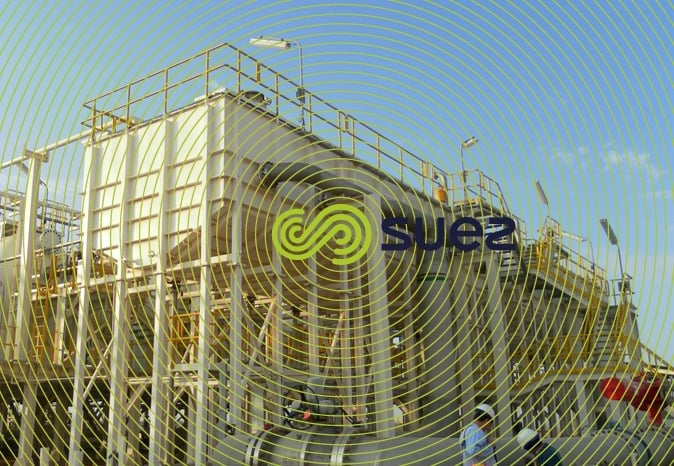


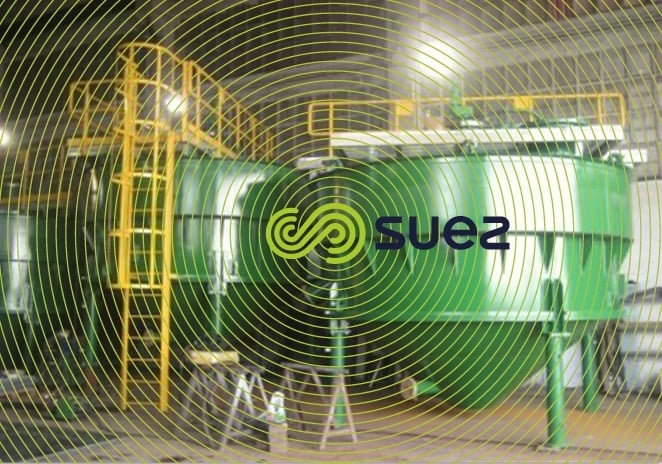

Based on the scheme, a gas field water treatment unit was installed in the North Sea. The process includes a CPI oil separator, stripping of organic compounds, dissolved air flotation followed by biological treatment allowing 30 m3/h to be treated and meeting very stringent discharge to the sea standards, particularly for BTEX compounds.
processing seawater for the purpose of re-injection
Various clarification criteria are significant depending on oil field permeability, e.g.:
- 98 % of particles > 2 mm eliminated;
- turbidity < 0.5 NTU or even 0.2 NTU;
- more rarely SDI < 3 (fouling index see treatability tests);
whereas the seawater can come from the coast or an estuary with significant levels of suspended solids, it can also be from offshore and, in that case, be low in suspended solids (< 1 mg · L–1).
The two potential treatment lines are very similar.
- coastal water (platform or offshore) – figure 31, the sedimentation stage being either clarification or rapid flotation (Rictor, see flocculators – settling tanks – flotation units).

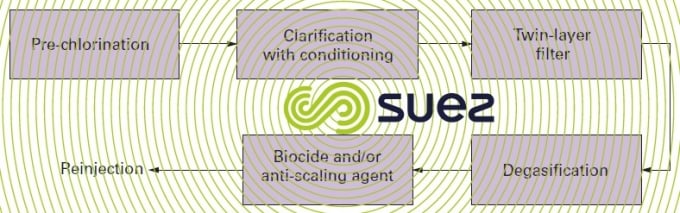

- offshore platform – figure 32.
Usually extracted at depths of 20 or 30 m below the surface, as this water no longer contains significant suspended solids (< 2 ppm), filtration, whether or not preceded by coagulation, is adequate.

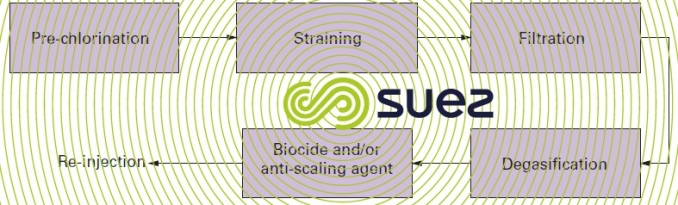

Bookmark tool
Click on the bookmark tool, highlight the last read paragraph to continue your reading later
