paper and cardboard manufacturing
Reading time:(including integrated paper mills producing mechanical pulp and/or de-inked pulp)
The great diversity of raw materials used and the variety of papers and cardboards produced requires a good knowledge of production systems in order to adopt, wherever possible, the principles established in plant design - general:
- internal treatment and recycling (short circuit);
- specific pre-treatments;
- optimised final treatment process (water + sludge) including any recycling (long circuit).

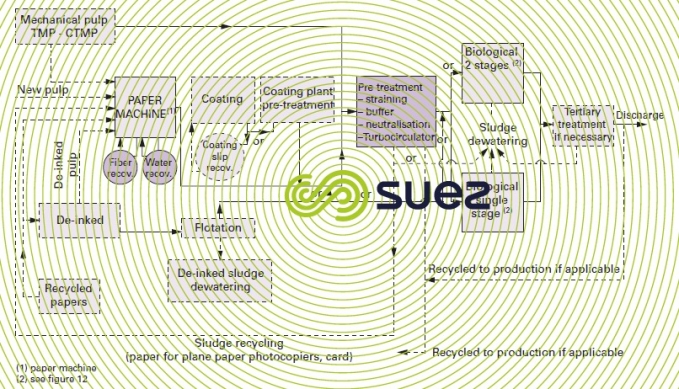

internal treatment and recycling (short circuit)
The paper industry is a heavy water and energy consumer and, because it uses expensive raw materials, internal recycling is essential. E.g. :
- fiber recovery from the paper machine (flotation, sedimentation, multi discs…), and occasionally coating slip through ultrafiltration;
- water recycling (savings on water and especially energy for heating) at various points on the paper machine or during the manufacturing process, the amounts and the quality of the water recycled being dependant on the type of paper manufactured.
specific pre-treatments
Depending on the paper mill type (whether or not integrated), the raw material used (new pulp or recycled paper) and the type of paper manufactured (news-print, magazine, printing-writing, tissue, coated, special, etc.), specific pre-treatments will be required:
- plain paper for photocopiers, cardboard from recycled paper: fine straining for removing plastic, staples, varying detritus;
- integrated machine (mechanical pulp, TMP, CTMP ): bar screening, grit removal (particles of wood, sand, etc.);
- coated paper: pre-treating coating unit concentrated water to break up the emulsion;
- de-inking: flotation applied to water produced by de-inking, dewatering deinking sludge.
optimised final treatment process (water + sludge) including any recycling
The specific pre-treatments described above having been completed, the treatment line will usually include:
a primary treatment
This treatment comprises:
- a preliminary pre-treatment;
- safety straining/bar screening;
- an equalisation tank (flow rate peaks linked to system drainage, changes in manufacture, etc.);
- neutralisation (belt chemical wash);
- sedimentation (Turbocirculator, flotation…);
- cooling if required.
a biological treatment
All the techniques described in chapters biological processes and methane fermentation are applicable, bearing in mind specific aspects dictating the choice of processes or technologies, e.g.:
- fiber fouling capacity;
- high calcium concentration levels (danger of scaling);
- latex that has not been pre-treated;
- presence of abrasive matter (TiO2, CaCO3, kaolin…);
- salinity (corrosivity).
The biological treatment can be executed in one or two stages depending on the capacity, the required effluent quality, space constraints, etc. Figure 12 indicates the various potential treatments and the final COD that can be achieved.

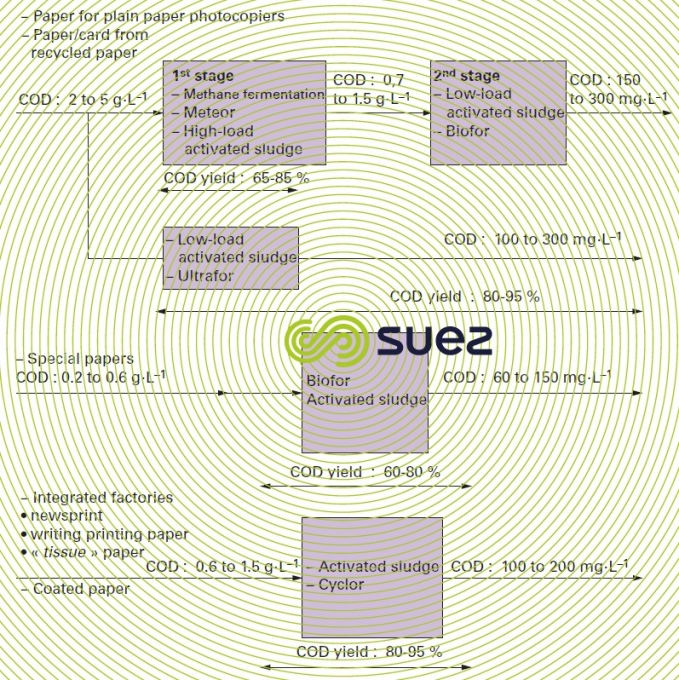

a tertiary treatment
A supplementary treatment may be necessary to reduce specific contaminants: suspended solids, hard COD, colour, etc. Potential processes that can be applied are those described in tertiary treatment, trequiring case-by-case assessment for each application.
a sludge treatment
Primary sludge contains fibers and mineral matter (generated by recycled paper or added during manufacture). The respective proportions of MM /fibers will vary depending on the type of output and on the level of internal recovery.
Primary sludge is:
- either recycled during the manufacturing process (manufacturer of plain paper for photocopiers for instance);
- or dewatered separately or combined with biological sludge, considering that it only accounts for 5 to 15% of the total sludge.
The various dewatering, drying or incineration processes used are those described in chapters liquid sludge treatment and dewatered sludge treatment, recognising that technical-financial optimisation will depend on the final objective as well as on the sludge composition (fibers, mineral matter, biological and tertiary sludge).
an odour control system
The treatment of paper mill wastewater should not generate any particular odour emissions but conventional precautions need to be taken in some cases:
- methane fermentation gas system (sulphides created by reducing sulphates);
- sludge dewatering unit.
Figures 16 to 20 illustrate the foregoing using a few typical examples.

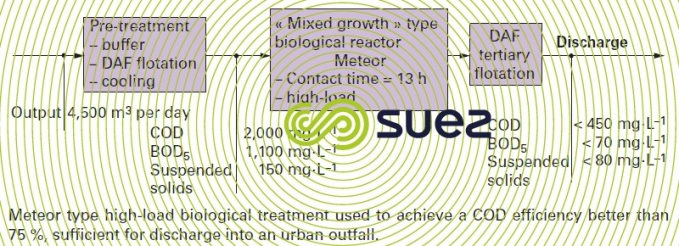

Bookmark tool
Click on the bookmark tool, highlight the last read paragraph to continue your reading later
