permeation processes
Reading time:gas permeation
A gas mixture can be depleted or enriched through action on the diffusion rates applicable to these constituents within the membrane’s dense matrix under the pressure gradient effect.
Examples:
- recovering oxygen from a mixture of hydrocarbons (figure 63-a) in the oil industry or from gas blowdowns when producing ammonia;
- enriching the nitrogen or oxygen levels in air.
degassing membranes (de-oxygenation)
Permeation membranes that are not water permeable but that are oxygen permeable and which, under the effect of a pressure gradient (vacuum) or of a downstream crosswash (chemical gradient), will allow the oxygen dissolved in the water to migrate to the downstream compartment without requiring the water to be brought into contact with any stripping or chemical products (scavengers) and, therefore, without running any risk of re-pollution. These membranes are being increasingly used, in one or more stages in series, in ultra pure water circuits for lowering dissolved oxygen to the ppb now frequently demanded. Hydrophobic micropore membranes are used for this application.
Similarly, to make water less aggressive these membranes are used to remove the carbon dioxide it contains. In industry, membranes naturally find themselves at home as an alternative to CO2 removal techniques using atmospheric air (or a stripping tower). In a resin-based mineral removal process, CO2 removal is often included upstream to the strong basic anion exchange resin process.
In a two-stage osmosis system and in order to produce water with low conductivity properties, near-total CO2 removal is compulsory between the two osmosis stages. This can be carried out using soda which will transform CO2 into hydrogen carbonate.

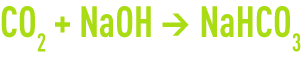
For this application atmospheric air stripping is not suitable. Indeed, this technology leaves a residual of CO2 of around 12mg/L after air stripping, which corresponds to the conductivity of 4.4µS/cm of CO2 alone.
Using degassing membranes in a reverse osmosis processes is a more elegant technique but requires heavy investment. However, it does dispense with having to use a hazardous chemical, i.e. soda which also causes salinity between the 2 stages of reverse osmosos.
pervaporation
Pervaporation membranes are dense skin, composite membranes.
When a negative pressure is applied to the downstream side of this type of membranes so that we have a vapor tension that is lower than that of one of the solutes in the solution in contact with the upstream side of the membrane, we will see this solute undergo selective transfer through the membrane as a gas. This solute can be recovered if necessary by condensating this gas.
Examples :
- alcohol dewatering: we can recover absolute alcohol by selectively transferring water vapor through a hydrophilic membrane (figure 63-b) (e.g. polyvinyl alcohol);
- remove THMs from drinking water: similarly, we can selectively diffuse these organic compounds through a hydrophobic pervaporation membrane (e.g. silicone).



membrane distillation (cf. figure 64)
Again, by creating a partial vacuum on the downstream side of a micropore membrane, we can create a system that :
- will oppose the migration of the liquid phase circulating on its upstream side provided that the pressure differential through the membrane remains lower than the capillary pressure through the membrane; in practice, porosity of less than 0.8 microns for hydrophobic membranes means that we can apply 1 bar pressure differentials without causing the water to permeate as a liquid;
- on the contrary, will allow water vapor through the membrane. As it condensates, this vapor produces extremely pure water; in effect only other volatile components can pass through the membrane at the same time as the water.
Some industrial systems operate using this principle. However, they do retain the energy hungry properties of single-stage distillation systems, see chap. degasification, odour control, evaporation. Conversely, organic membranes will be required in order to avoid the corrosion phenomena found in evaporators.
Potential application: concentrating industrial (toxic…) effluent before incineration or crystallisation.

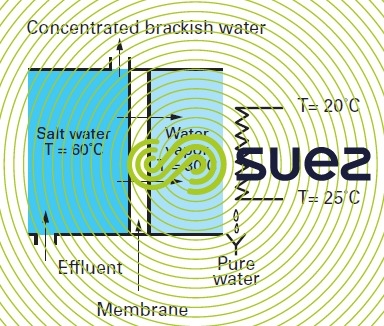

Bookmark tool
Click on the bookmark tool, highlight the last read paragraph to continue your reading later
